11 April 2024
- UK’s National Composites Centre has partnered with Cevotec to demonstrate a proof-of-concept that has the potential to reclaim up to 80% of dry fibre manufacturing waste from landfills.
- The recycling trial, using Fibre Patch Placement technology, offers an improved circularity solution that benefits from maximising the mechanical properties of waste material from the earliest stages of aerospace manufacturing.
Engineers at the National Composites Centre (NCC) have successfully demonstrated the potential to recycle up to 80% of carbon fibre material from the earliest stages of aerospace manufacturing as alternative feedstock.
Background
Contributing over £22 billion to the economy, the UK’s aviation network is the largest in Europe, and second globally. The sector’s rapid growth necessitates lighter, cheaper aviation systems produced as much as 10 times faster than current rates. Net zero ambitions are also mandating change through regulation, policy, and public opinion. With landfill tax increasing and energy recovery (incineration) less than ideal, the next sustainable solution must include the investigation of more efficient, cleaner, and smarter manufacturing from cradle to gate.
Challenge
The highly regulated aerospace industry is subject to strict standards and regulations to ensure the safety and reliability of aerospace components. This includes stringent criteria for aviation systems such as wings to be cut in a precise manner. As a result, a typical primary ply kit discards up to half the allocated virgin materials during ply cutting. In a bid to retain the value of the aerospace-grade discard, experts at the NCC explored the viability of recycling dry carbon fibre manufacturing waste into feedstock for a secondary manufacturing process that can produce high performance components from shorter fibre material.
Innovation
Munich-based Cevotec uses additive manufacturing technology for the automated production of geometrically complex composite components. Their Fibre Patch Placement (FPP) technology utilises fibre material patches in the lay-up of products. As such, the NCC team realised a novel opportunity to cut biaxial non-crimped fabric (NCF) carbon dry fibre manufacturing waste into defined patches to maximise the potential yield for alternative feedstock. Guided by virtual nesting trials, experts at the NCC utilised an automated ply cutter fitted with a rotary cutter to produce the precise patches required for FPP manufacturing.
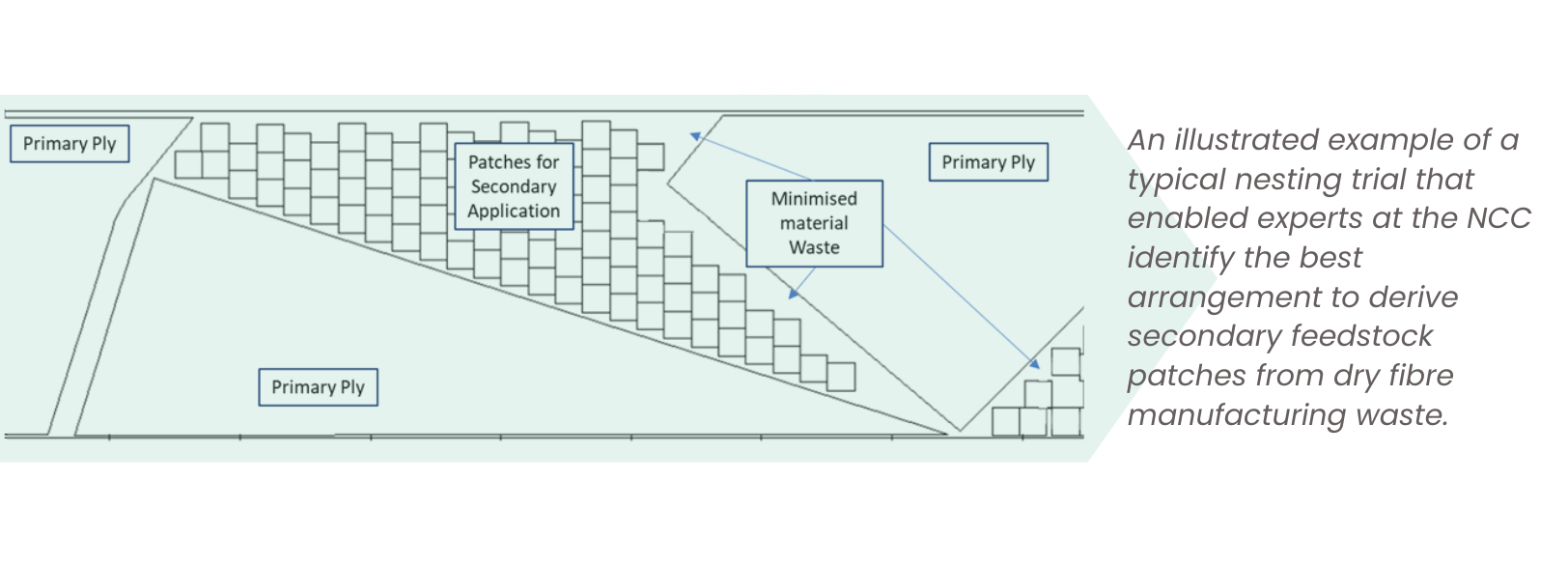
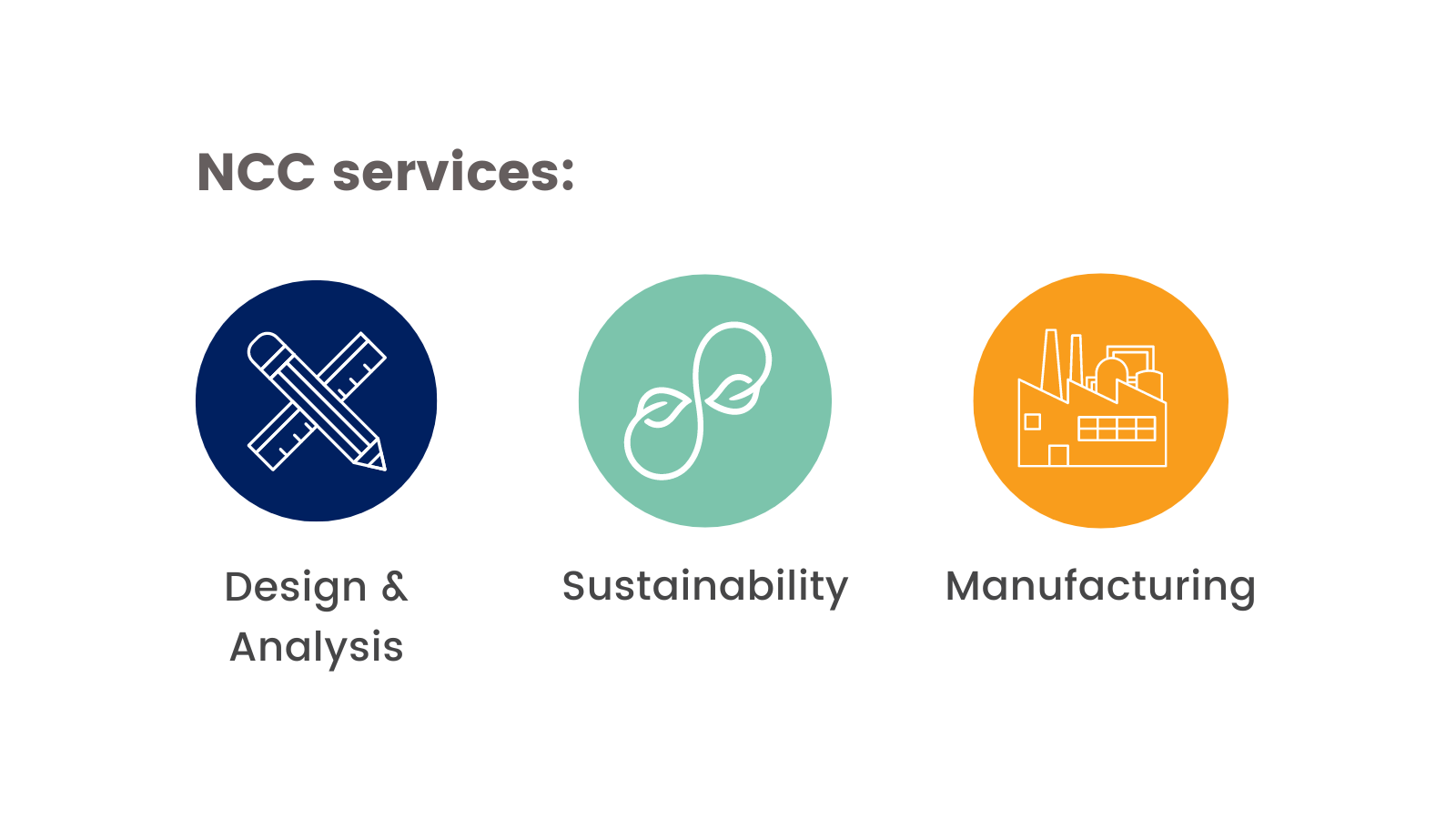
Results
Supported by project sponsors Airbus and Spirit, engineers at the NCC have successfully manufactured a semi-complex demonstrator from dry fibre manufacturing waste – reclaiming almost 40% more virgin materials from the ply cutting of biaxial NCF carbon dry fibre.
Using Cevotec’s proprietary software to design the laminate for the demonstrator with the secondary feedstock patches, the NCC were able to consider infusion and cure techniques to demonstrate a proof-of-concept that an established FPP process could deliver up to 80% utilisation rate from material waste.
Utilising FPP also benefits from retaining longer fibre lengths than most other recycling options. With longer fibre lengths, still in the same weave as virgin material, the opportunity for high value secondary use is possible.
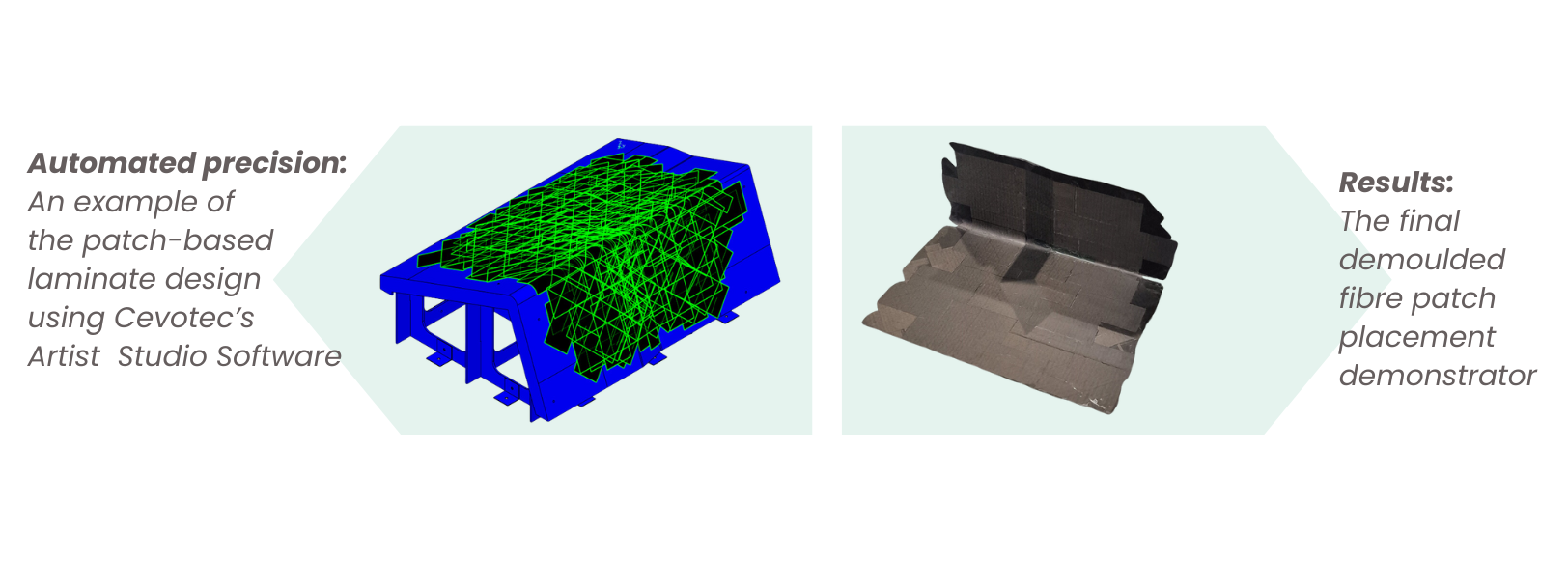
Impact
Future aircrafts are likely to see even more adoption of composites than aircrafts like the A350, with a greater emphasis on higher rate, lower cost and significantly improved sustainability during manufacture. Predicting a future manufacturing rate of 75 aircraft per month and using a representative pre-preg wing component, the NCC projected an annual average of ply cutting material waste to be in excess of 16,200kg. However, recycling the ply cutting material waste as FPP feedstock could drive down uncured waste destined for landfill to less than 4,400kg. This potentially diverts some £912,000[1] worth of material from a single component’s waste towards alternative secondary products each year. For an aircraft, these products could include fuselage and cabin structures, such as window frames and cabin liners.
With composites making up more than 50% of next generation aircraft by weight, the environmental and financial savings could be significantly increased if FPP secondary feedstock was considered for more than just a single wing component, per example here. Being automated, the FPP process is also perfectly suited for integration with digitally enabled manufacturing. The existing system already includes aspects of in-process verification to ensure optimal material use and part assurance. With the ability to use a high-fidelity simulation, modelling, data analytics and machine learning to study the impact of variables, digital twin technology could assist in more accurate component life prediction. This could enable more accurate repair with significantly closer to “as-new” performance of the repaired component.
Next steps
These preliminary findings offer an encouraging outlook for more sustainable aerospace manufacturing, with the opportunity to explore converting dry fibre manufacturing waste into FPP secondary patches for other highly regulated industries.
The next phase involves refining FPP designs for more complex components; exploring stability, varied materials and maximising secondary feedstock patch value. The NCC is looking to work with industry partners to explore testing the final demonstrator in a real-world setting. Future work will explore the full range of sustainability and economic factors with dry fibre manufacturing waste, using the NCC’s Life Cycle Analysis and Life Cycle Costing capabilities. Following on from this development of dry NCF fabrics in addition to the original prepreg fabrics and tapes, the team is now exploring more composite material types and working to validate performance of complex components.
Florian Lenz, Technical Director for Cevotec says:
“Fibre Patch Placement technology offers a new option for flexible and productive composite manufacturing, generating value from material scrap. Adapted to the size and complexity of a component, the technology works additively in sensible increments via fibre patches. This process enables automation for complex 3D shapes, multi-material laminates and local reinforcements that comply to lightweight product needs and quality standards.”
Tim Young, Head of Sustainability at the National Composites Centre says:
“To achieve net zero, we need to invest in new ways to reduce and remove carbon emissions from how we consume it: from concept, design, and manufacture to end-of-life recycling and disposal.
“At the National Composites Centre, our sustainability expertise with leading engineering capabilities supports businesses to identify opportunities to reduce their environmental footprint across the value chain. Be it minimising energy use to extracting the maximum potential from every strand of high-performance fibre, our ongoing research and development prioritises circularity to remove the pressure placed on our environment through landfill.
To get involved with developments in this space, reach out to: [email protected]
[1] Based on estimate of £23/m^2 or £77/kg