13 November 2023
The CERCOMP UK collaborative research project advances aircraft propulsion technology, while paving the way for a secure supply of affordable advanced ceramic composites in the UK.
Globally, the ceramic matrix composites (CMC) market is estimated to grow to USD22 billion by 2030. This substantial rise is attributed to the emerging need for engineering solutions within high-temperature, extreme and harsh environments. In support of developing a robust and cost-effective CMC supply chain to advance aircraft propulsion systems in the UK, the Aerospace Technology Institute (ATI) initiated the CERCOMP UK project. The strengths of the High Value Manufacturing Catapult (HVMC) consortium - led by the National Composites Centre with the University of Sheffield Advanced Manufacturing Research Centre (AMRC) and the Manufacturing Technology Centre (MTC) – was harnessed to increase UK’s technology readiness levels (TRL) of a collection of CMC-related technologies.
Challenge
Being a third of the weight of metal alloys, coupled with the ability to withstand up to 1,000C means oxide-based CMCs enable jet engines to run more efficiently at higher thrust. For some primes, the technology is expected enable a 25% improved thrust with 15% better fuel consumption, delivering lower emissions and greater durability. However, CMCs’ utility for the defence sector means such advanced ceramics technologies are often export-controlled with development dominated by the USA, Japan, France, and Germany. As a result, the high-cost dependency on international supply chains has prevented widespread investment in CMC technology until recently.
World Class R&D
Engineering experts on CERCOMP UK focused on:
- Processing and materials data: Benchmarking product performance to provide UK industry with the knowledge required to manufacture new CMC products.
- Identifying low-cost materials and manufacturing options for CMCs.
- Machining: Assessing benefits and drawbacks of both conventional and novel CMC machining and methods to give industry confidence to use CMCs to develop their components.
- High-rate and low-cost non-destructive testing (NDT): Establishing best practice of CMC manufacture methods to ensure faster and more successful product development that meets expectations and with lower scrap rates.
- Repairability and joining: Assessing the viability and effectiveness of repairs to restore structural integrity and extend the life of CMC components, therefore reducing their impact on the environment.
-
CMC life cycle assessment and costing
-
Exploring the development of a UK-based materials, engineering, and product supply chain for CMCs.
-
Assessing the health and safety aspects of factory facilities requirements during manufacturing and machining.
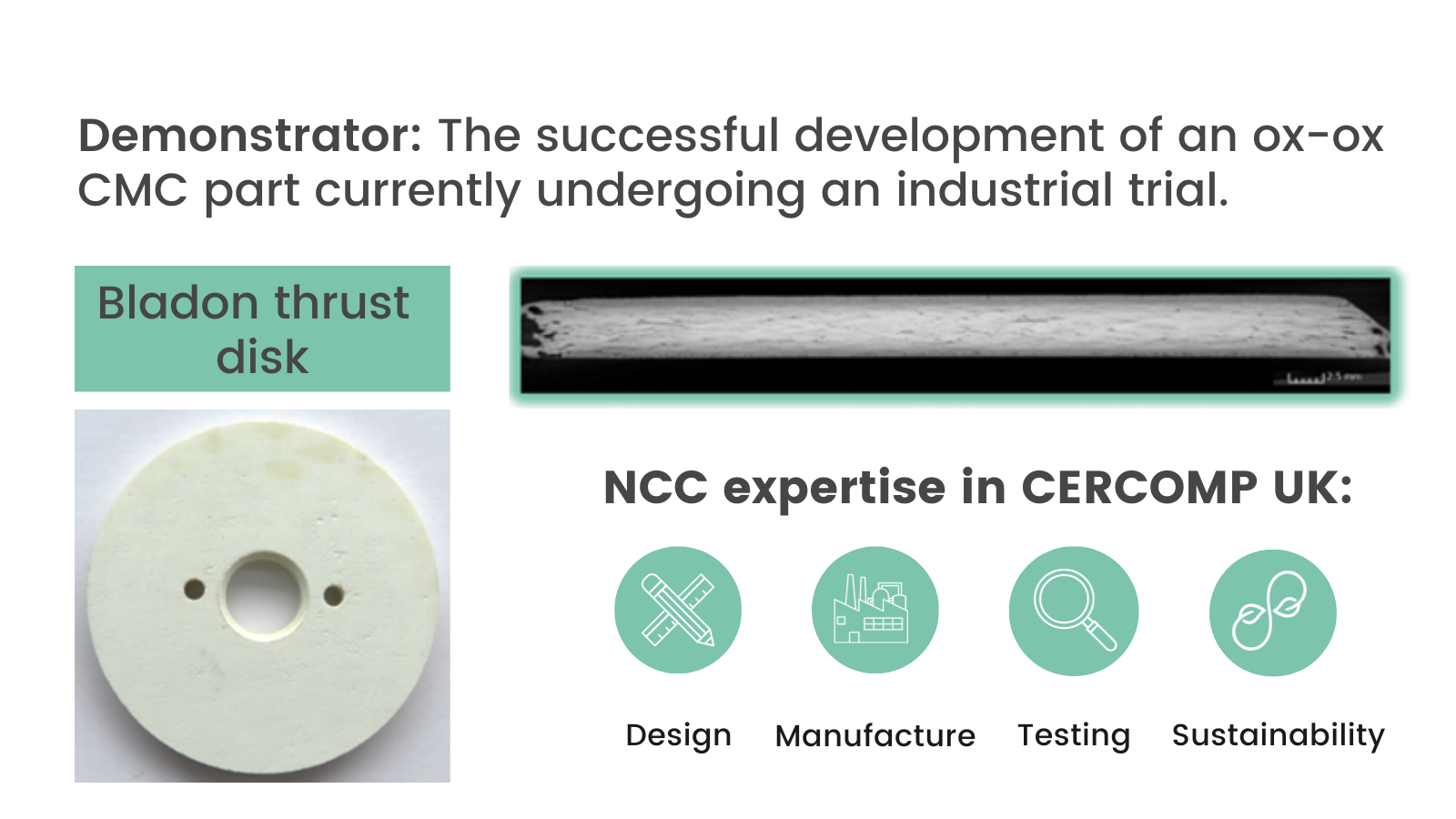
Demonstrator
The two-year sprint study enabled the HVMC consortium to jointly develop a CMC disc demonstrator. With material manufactured at the NCC and precise machining by both the AMRC and MTC, the 39mm demonstrator has been designed to operate under heavy thermal cyclic conditions.
The demonstrator is currently undergoing a trial with industrial partner Bladon Micro Turbine to learn its capability in challenging real-world conditions. Results are expected to demonstrate ox-ox CMCs’ long-term stability, wear, and chemical resistance under elevated temperature within highly oxidizing environments.
Impact
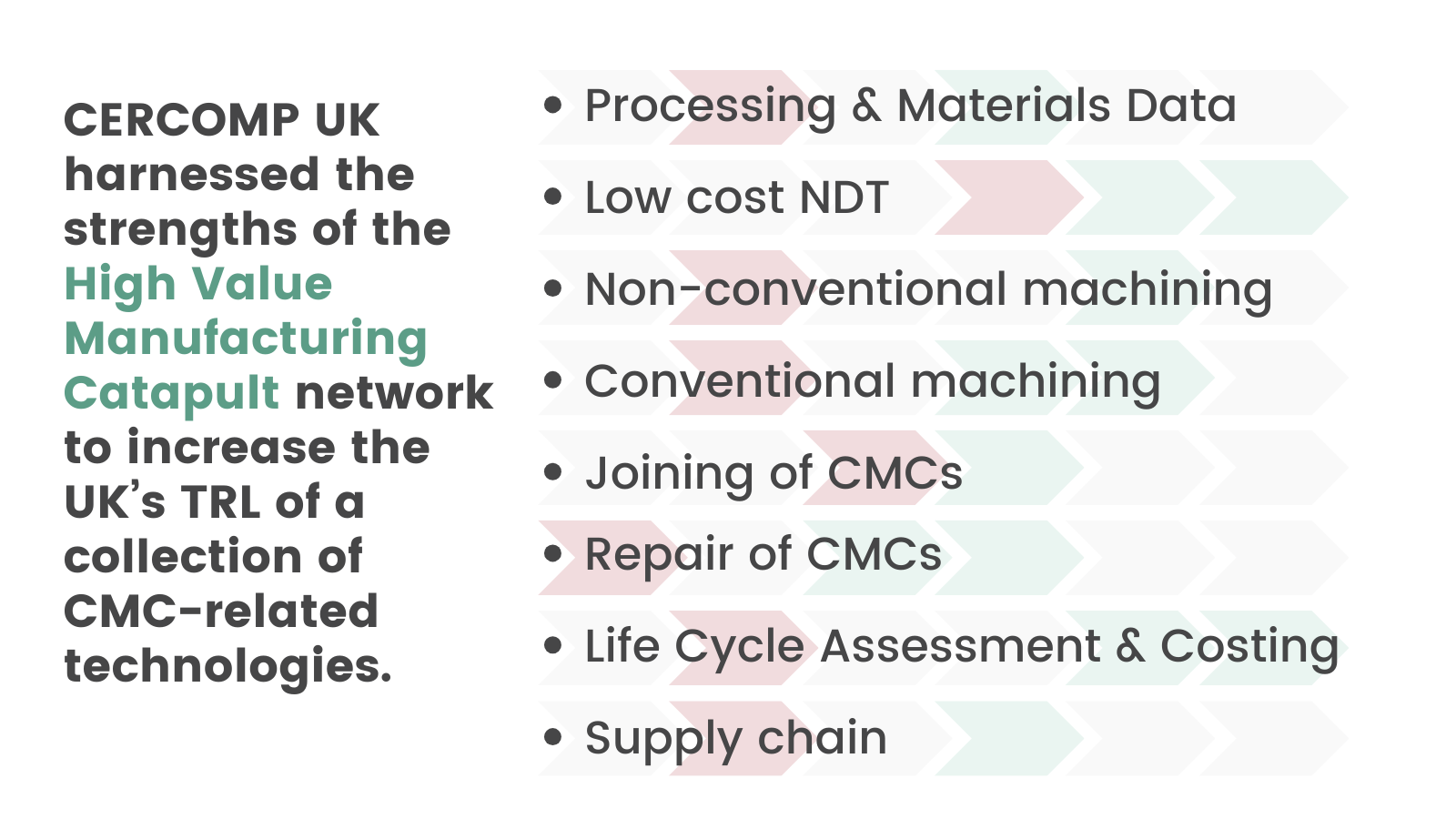
The CERCOMP UK project successfully identified and built a supply chain network capable of delivering a range of technology services required to manufacture CMCs. This home-grown supply chain network can now be utilised by the UK industry to manufacture next generation CMC components and exploit the advances made during this programme in manufacturing, materials data, machining, and NDT.
For the HVMC consortium, the knowledge developed throughout CERCOMP UK builds towards their capability as a lead technology cluster to help develop, expand, and diversify UK’s CMC market offerings in key industrial sectors beyond aerospace, such as defence and space.
Next steps
Developing CMCs within the UK requires access to a wide variety of specialist equipment and knowledge. Therefore, the NCC is launching a CMC working group to promote collaboration and communication between UK specialists. The creation of a UK-based CMC network can then be exploited by industry primes to develop the nations next generation advanced materials.
The recently opened AMRICC centre in Stowe, UK, houses an array of advanced sintering furnaces. These open access facilities bring new processing capability to UK research which is essential for manufacturing next generation materials for extreme environments.
The NCC is also collaborating with Lucideon to provide a comprehensive range of services in the use of oxide and non-oxide ceramic composite materials for a variety of applications. Lucideon will focus on providing analysis and evaluation, and supporting the development of advanced materials and applications, with the NCC concentrating on full system and product design, and industrial scale development.
Virtudes Rubio, Principal Research Engineer at the National Composites Centre says:
"CERCOMP UK was an integral foundation towards readying the UK for end-to-end engineering solutions for high temperature, extreme environment applications. The NCC’s ongoing collaboration with industry partners such as Lucideon aims to address the challenges around security or supply and cost effectiveness of CMCs to drive innovations in the UK for aerospace and beyond."
If you would like to learn more about the potential of CMCs, please contact [email protected]