06 September 2023
The National Composites Centre offers a faster, lower cost and more sustainable solution to enable timely business expansion to support the local electric vehicle supply chain needs.
To meet the UK Government’s net zero commitment to end the sales of new petrol and diesel cars by 2030, the automotive industry is ramping up efforts to increase the production of battery-powered vehicles. This rising demand is putting pressure across the UK electric vehicle (EV) supply chain. Capitalising on this EV opportunity with funding support from Innovate UK EDGE, electric vehicle specialist Watt Electric Vehicles turned to the National Composites Centre (NCC) for an affordable, right-sized solution to scale-up production of their composite battery trays.
Results
Drawing on the NCC’s end-to-end engineering expertise, a team of skilled manufacturing technicians focused on the consolidation and cure process of the EV trays. Small-scale trials were conducted, comparing the manufacturing process flow, timing and cost using conventional options such as (1) Watt’s existing standard vacuum bag, (2) an industry-standard hydraulic press, and (3) a flexible reusable vacuum bag (RVB). Findings from these manufacturing trials were supplemented by a desk-based study investigating estimated rough order of magnitude, capital expenditure as well as component and labour costs. With careful considerations of the SME’s budget and scale-up needs, the NCC recommended the reusable vacuum bag as the ideal fit-for-purpose solution for the growing business.
Challenge
The UK-based OEM produces lightweight aluminium and thermoplastic EV platforms with a fully integrated battery case. Adjustable to fit different vehicle architectures and capable of accommodating rear- (RWD), front- (FWD) and four-wheel drive (4WD) with different suspension concepts, the hybrid material plate is lightweight, offers great impact resistance, and does not constrain the vehicle size or design. The barrier to business growth was a complex manufacturing process that was both labour and time intensive, thereby limiting production rates.
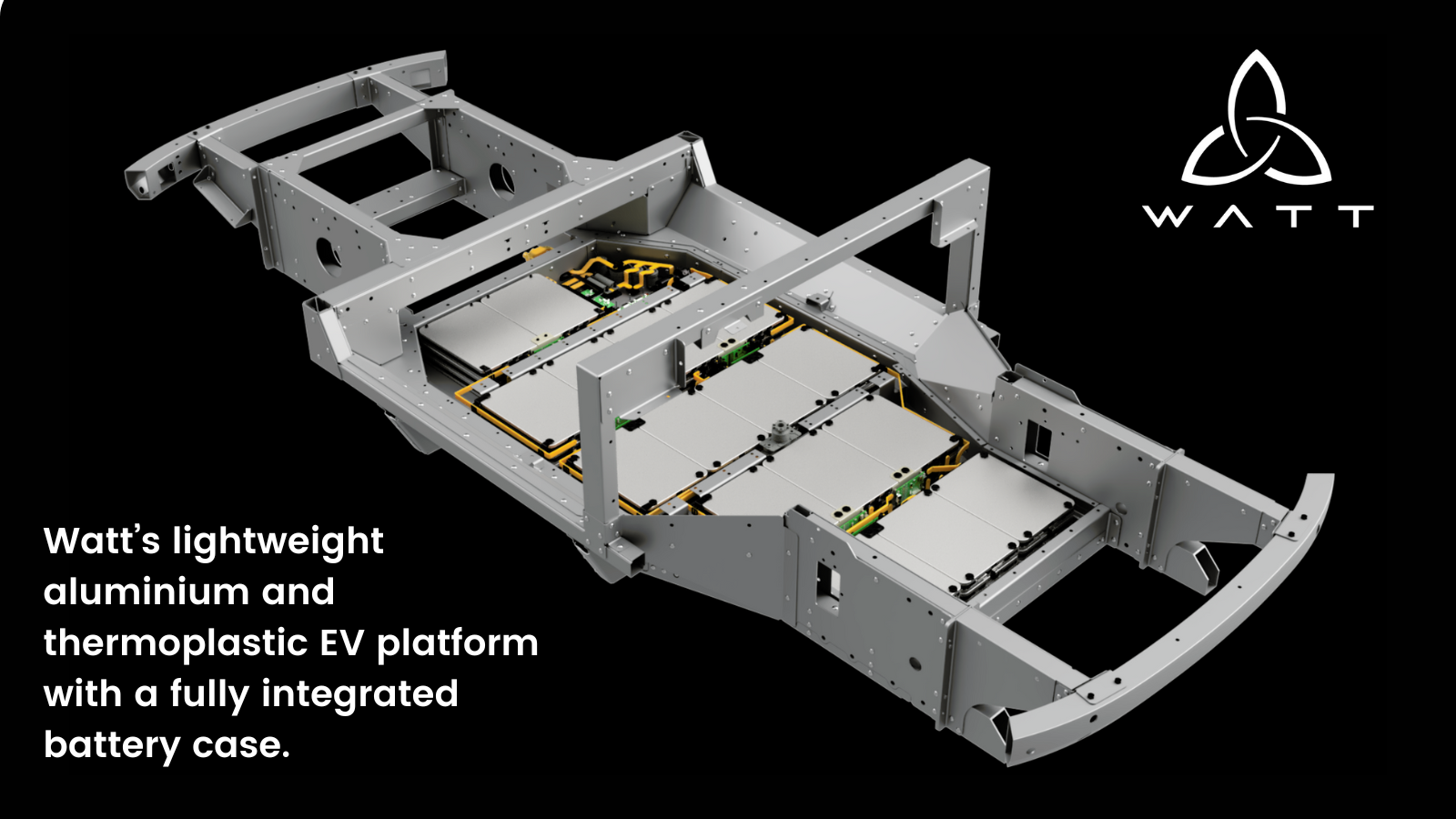
Impact
In a test setting, the innovative solution offered a faster, more cost-effective, and potentially more sustainable alternative to Watt’s current way of manufacturing the part:
- Faster: Cuts per-part production duration by at least ten-fold a day.
- More cost-effective: Considerably cheaper than the hydraulic press; when compared to the existing method, the cost of the RVB can be recouped within the first production run.
- Reduces consumables: Eliminates film bag waste as reusable options have the potential to withstand over 100 cycles.
Next steps
Watt Electric Vehicles has recently completed round 1 of investment funding, earmarked for the production of their next-generation EV prototypes. Their Alpha phase development vehicles will incorporate the manufacturing solution proposed by the NCC. Furthermore, ongoing efforts include investigations into the implementation, embedded energy monitoring, and conducting a comprehensive life cycle assessment (LCA) to evaluate the sustainability impact of the part manufacture.
According to Alasdair Mustard, Program Manager, Watt Electric Vehicles:
"We went into the project with the expectation that the outcome would justify investing in the costly gold-standard hydraulic press system. However, the NCC’s careful consultation, shared learning and recommendations have given Watt EV the confidence to investigate a cheaper alternative that we had not considered – still delivering increased production, yet in a potentially more sustainable manner.
"These improvements are supporting our efforts to introduce the next-generation commercial EV, the eCV1, to the market."
Adding to this, Tim Woodhouse, Head of SME Delivery at the NCC said:
"At the National Composites Centre, our dedicated NCC Connect team connects SMEs with end-to-end engineering capability. This includes access to in-house expertise in design; material selection; validation and certification; manufacturing; digital engineering; maintenance; as well as end-of-life and circularity. By facilitating right-sized solutions to fit their business needs, we help manufacturing SMEs fast-track their next steps into business expansion."
The National Composites Centre is part of the High Value Manufacturing (HVM) Catapult network of research centres. For more information on how the NCC team can help the low-carbon vehicle community de-risk and drive innovative solutions to unlock their business potential, reach out to NCC Connect.
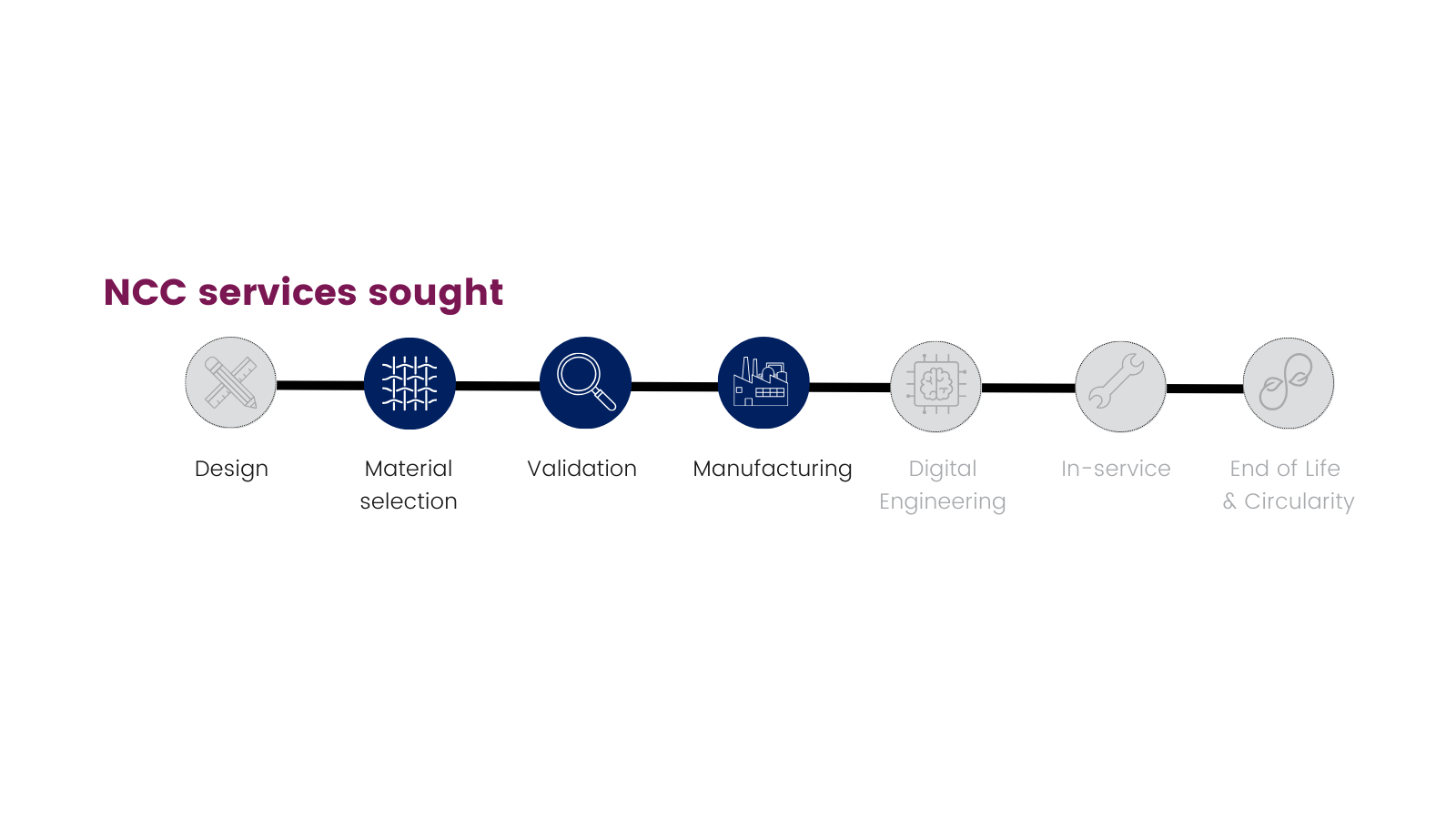