07 April 2025
The NCC explores a proof-of-concept offering a multi-repair solution that could significantly extend product lifespan and reduce environmental impacts. For the energy industry, the potential impact of application to wind turbine blades could generate substantial environmental and economic benefits for the UK.
Vitrimer materials are an emerging class of plastic that combine the durability of thermosets with the reprocessability of thermoplastics. Their ability to maintain performance while being repairable presents transformative potential for sustainable mass production.
The NCC, in collaboration with the University of Bristol (UoB), is spearheading the development of vitrimer materials to address an innovation gap. By leveraging new manufacturing methods such as modular infusion and fusion assembly, this partnership is exploring novel ways to repair damaged advanced materials, providing an alternative where current options are limited to invasive patch repair or worse, landfill scrappage.
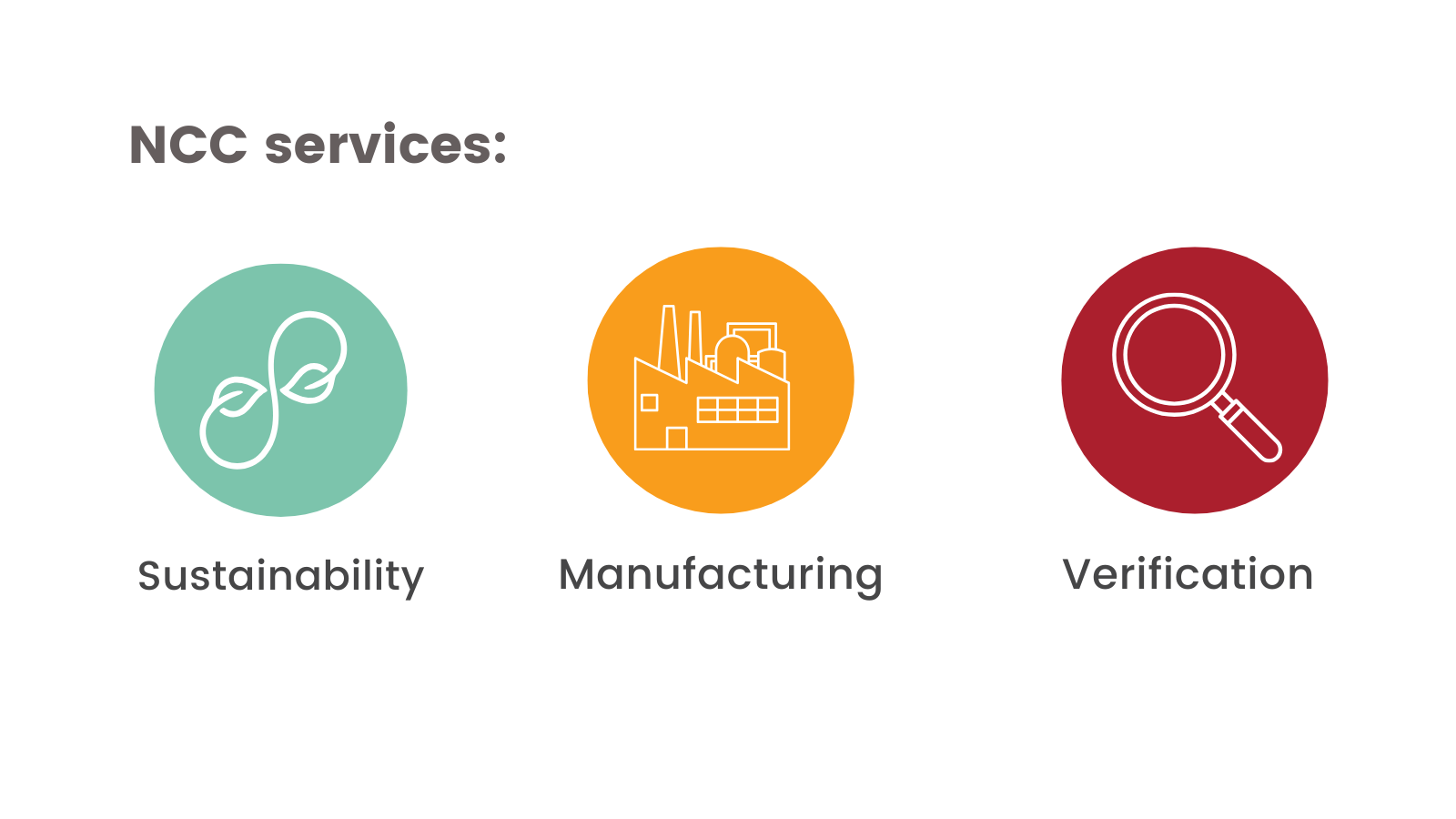
Challenge
The NCC’s technology pull-through (TPT) programme connects research with industry to enable innovation. This TPT project aimed to explore the next generation of advanced materials and tackle limitations in conventional advanced materials by:
- demonstrating innovative manufacturing and repair methods for advanced materials, and,
- highlighting the multi-functional potential of modular infusion techniques.
Innovation
In a world first, NCC utilised fusion manufacturing to demonstrate how vitrimer material properties can add adhesive-free bonding functionality to manufacturing processes. Furthermore, the same vitrimer material was utilised in a one-shot modular infusion to demonstrate the application of these future materials within existing manufacturing processes.
To simulate damage within a wind turbine blade, a T-stiffened assembly was pulled apart to complete failure. The damaged section was repaired using scalable induction heating methods, demonstrating how this material technology enables in-field repair of damaged components in larger structures.
This innovation represents a paradigm shift from current composite manufacturing processes towards new circularity enabling design for repair and design for end-of-life recovery.
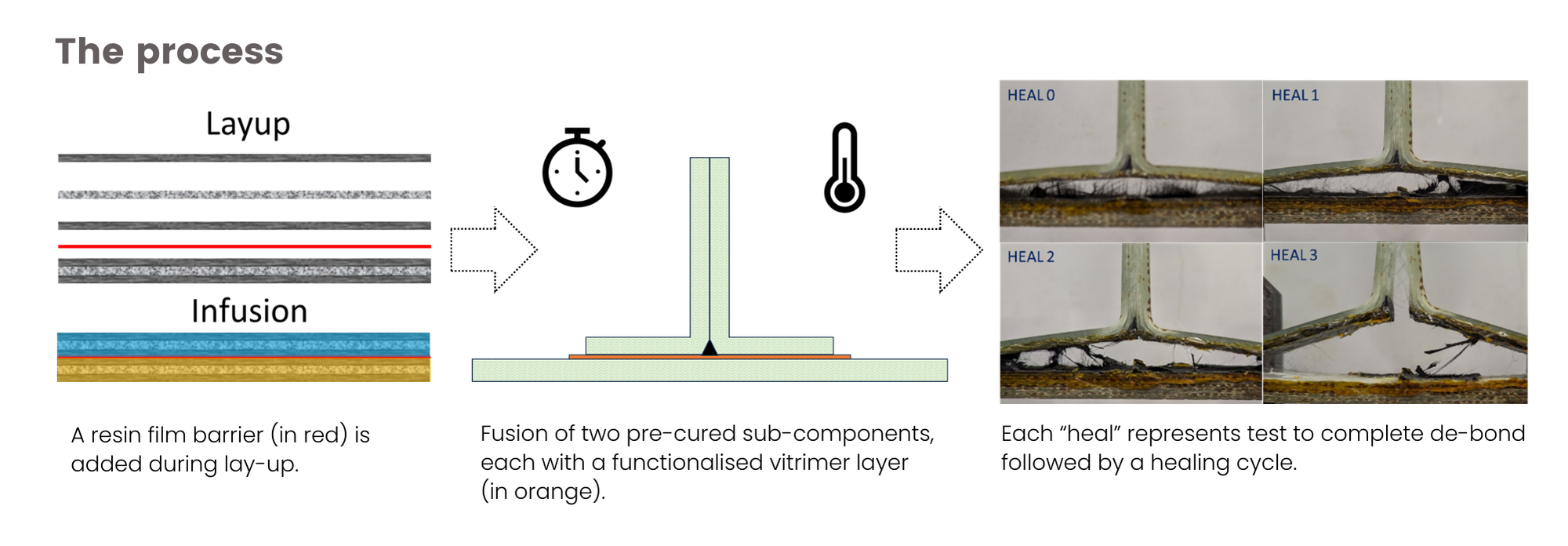
Results
Prioritising repairable solutions offers significant economic and environmental benefits. Key findings include:
- Service Life Extension: Leveraging both oven and induction heating methods mechanical properties were restored after complete failure. The healable interface component was successfully repaired three times, representing substantial life extension possibilities.
- End-of-life breakdown: It was demonstrated that structural elements could be separated upon heating of the healable interface creating opportunities to salvage and repurpose material that would have otherwise been discarded as waste.
- Reduced Environmental Impact: Considering manufacturing and repair processes only, a life cycle assessment (LCA), employing this repair technology instead of replacements, showed a 51% reduction in global warming potential (GWP).
Impact
Although the initial manufacturing of healable interface requires more energy, the ability to repair them rather than replace components makes this approach significantly more sustainable in the long term.
In the context of the UK Offshore Industrial Growth Plan— which projects £5.4 billion in economic growth over 10 years through wind turbine blade expansion — extending the lifespan of such components could generate substantial environmental and economic benefits for the UK.
Next Steps
Building on this successful proof of concept, the project team plans to:
- Further develop a vitrimer material formulation suited to composite manufacture processes,
- Demonstrate how salvaged materials can be recertified for second life applications,
- Conduct further research and testing, led by UoB, with manufacturing spearheaded by NCC, with an aim to bring the solution to market.
Dr Dmitry S. Ivanov, Associate Professor in Composites Manufacturing at the University of Bristol said:
“The Technology Pull-Through program not only advances early-stage concepts to the next level of readiness but also facilitates the dissemination of results to an industrial audience. This approach helps gauge industry interest while preserving background IP and enabling further academic research. Building on the success of this project and prior work, we continue to drive research at UoB, focusing on novel manufacturing concepts that integrate vitrimers into structures and leverage their unique properties to redefine manufacturing strategies."
Matt Scott, Chief Technologist for Strategy at NCC said:
“The NCC’s unique Technology Pull-Through programme bridges the gap between academia and industry, taking promising technologies from the lab and advancing them towards real-world application. With funded, managed 12-month projects, we provide the ideal environment to de-risk, scale up, and industrialise innovative, sustainable solutions.”
For more information on the TPT programme, reach out to our experts using the link below.