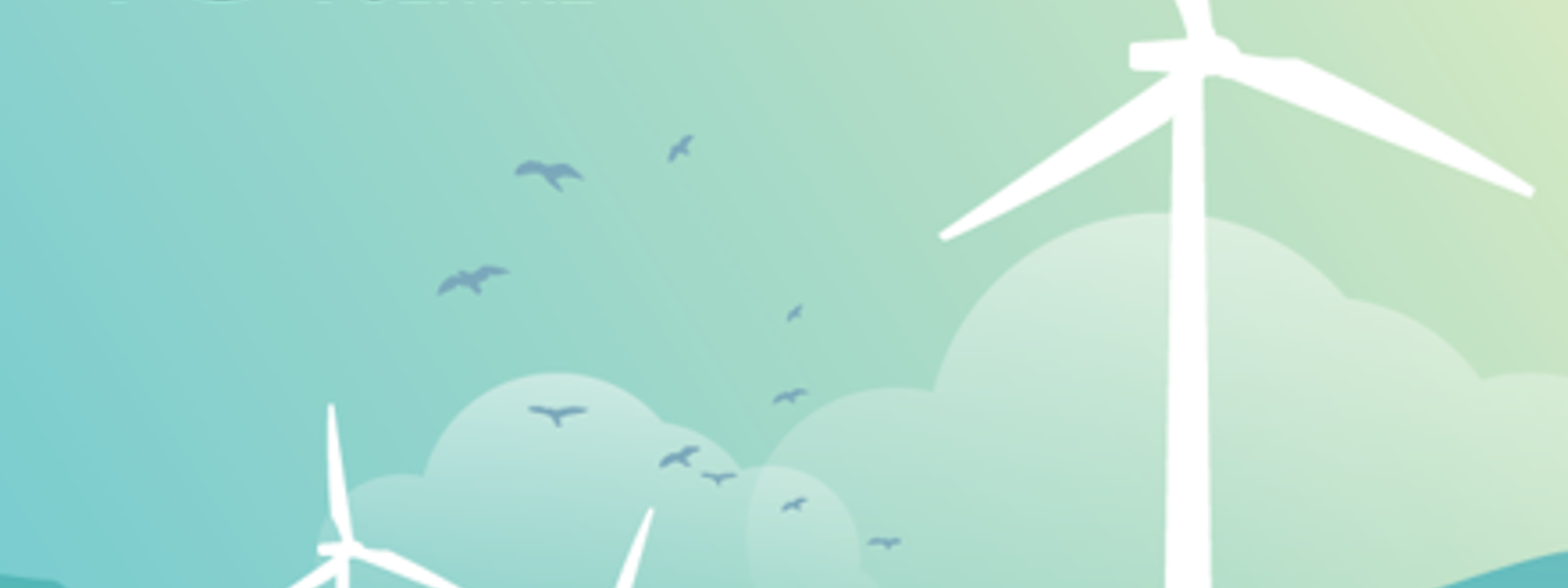
SusWIND: Establishing a viable UK-based circular market for the wind industry
SusWIND is a collaborative innovation programme focused on creating a viable circular economy for wind turbine blades. To enable this future state, SusWIND and its partners are developing methods and tools for assessment and scenario planning for three key facets of a future industry: Reclaim, Adopt and Develop. This extract from the SusWIND Annual Review 2023 looks at industry leading evidence that enables the bold decision-making needed to deliver industrial transformation at end-of-life.
Preservation of value is imperative once blades reach their end-of-life. As material value is inherently linked with its performance it is critical to reclaim the material in a low impact manner whilst maximising its properties, therefore preserving its value.
It is vital that the future industrial processes used to recycle large composite structures, such as turbine blades, reclaim both fibre and resin where it is sustainable and cost-effective to do so. However, the UK is not operationally ready to process end-of-life turbine blades to reclaim value from glass fibre composites. The green shoots of an industry are present and will be demonstrated in the SusWIND programme.
Challenge
The requirements for both recycling technologies and a supply chain should be determined by the economics and sustainability needs of the wind industry. The asset owners should use a data driven approach to understand which technologies should be developed, upscaled and industrialised by the emergent blade recycling industry. For the end-of-life (EoL) supply chain to function, the value associated with the reclaimable materials within blades and the benefits available to each actor in the chain needs to be understood. This covers every step from wind farm through to logistics, blade downsizing, repurposing or material reclamation and finally reprocessing into a consistent and marketable product.
Impact & Results
SusWIND has deployed a rigorous data-driven approach to understand the requirements of the industry so that it can provide a demand into the technology owners. This industry pull is critical to form a supply chain that best meets the needs of the asset owners. By taking this end-to-end approach SusWIND can help define the industry’s requirements and compare these against the capabilities of the various developmental recycling technologies to propose those that should be championed and upscaled.
When considering recycling, our technology landscaping and supply chain mapping activities made it clear that mechanical recycling and cement kiln co-processing are the only options at higher TRL but are still not available in the UK. Initial findings of a cradle-to-grave life cycle assessment of the blade incorporating various EoL options has shown that mechanical recycling and cement co-processing have the lowest GWP. For cement co-processing, however, the environmental impact depends heavily on the feedstock being replaced and will be the subject of further investigation in SusWIND.
Recommendations
Based on these results, SusWIND is recommending the following routes be scaled up and the supply chain built to support them:
A low impact reclamation for low value materials
- Where glass fibre reinforced composites are used in blades they should be processed via mechanical recycling or cement co-processing (if appropriate), as these routes are the lowest GWP options, highest TRL and are well suited to the all-glass fibre composite blades that will be coming to end-of-life in the next decade.
High value materials can be reclaimed via many routes
- High value carbon fibre composites should be separated from glass fibre composites and then recycled via pyrolysis or solvolysis. These technologies can reclaim a high-quality fibre and may in future reclaim the polymer fraction to offer additional benefits. Where this is done in conjunction with the recommended routes for glass fibre composites, this is termed “cement kiln+” and “mechanical+” (Figure 5).
- Processing carbon fibre composites separately from the glass fibre stream offers environmental benefit compared with combined processing. This is enabled through the offset of virgin material that is energy intensive to produce and holds true despite the use of a more energy intensive reclamation process.
- Carbon fibre reclamation technologies developing in other sectors still need to be proven for wind blades, however UK-based wind blade waste streams would not warrant a supply chain for approximately 15 years. Commercialisation of carbon fibre recycling and expansion of recycled carbon fibre reprocessing will require cross-sector collaboration to be viable.
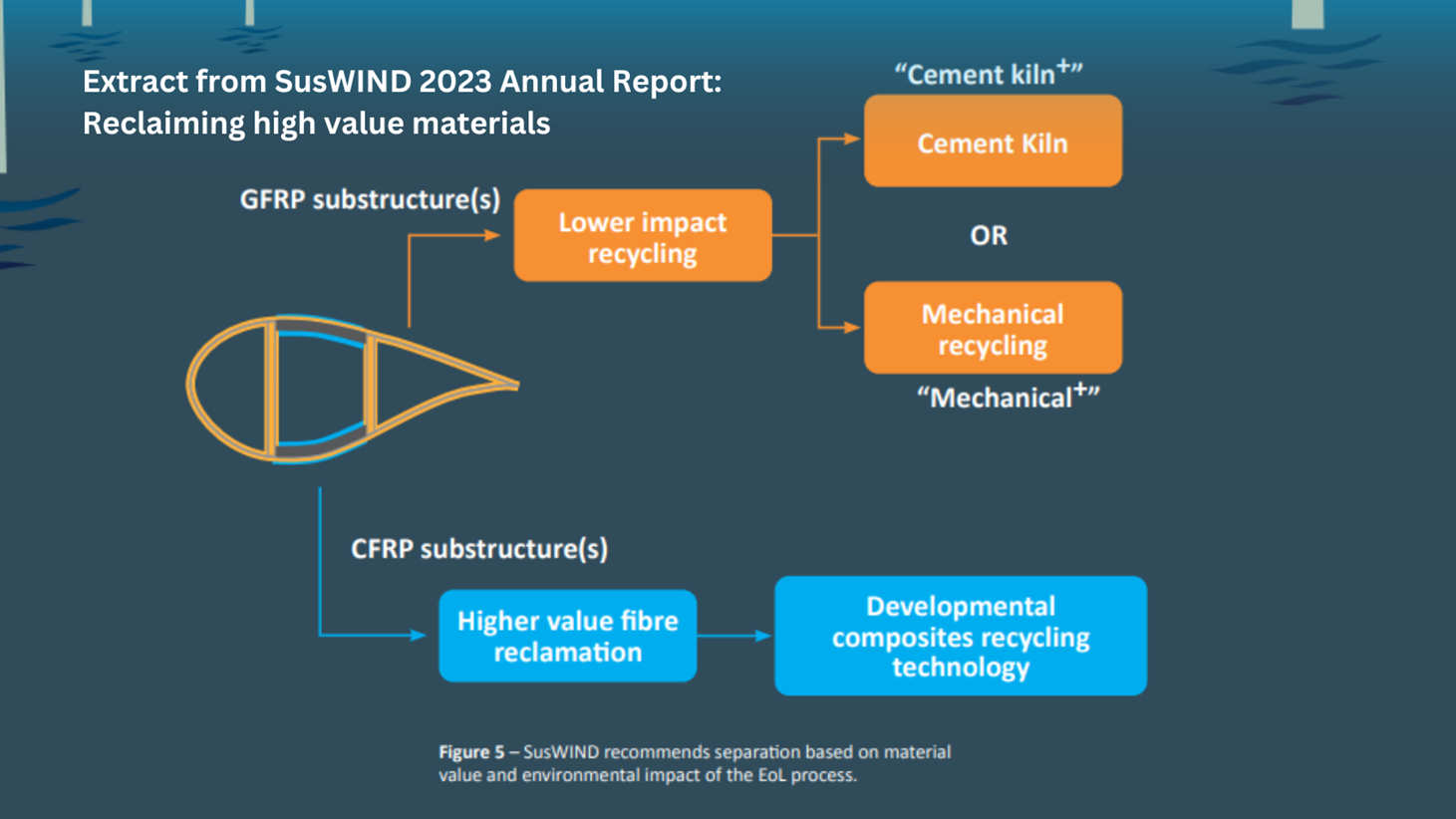
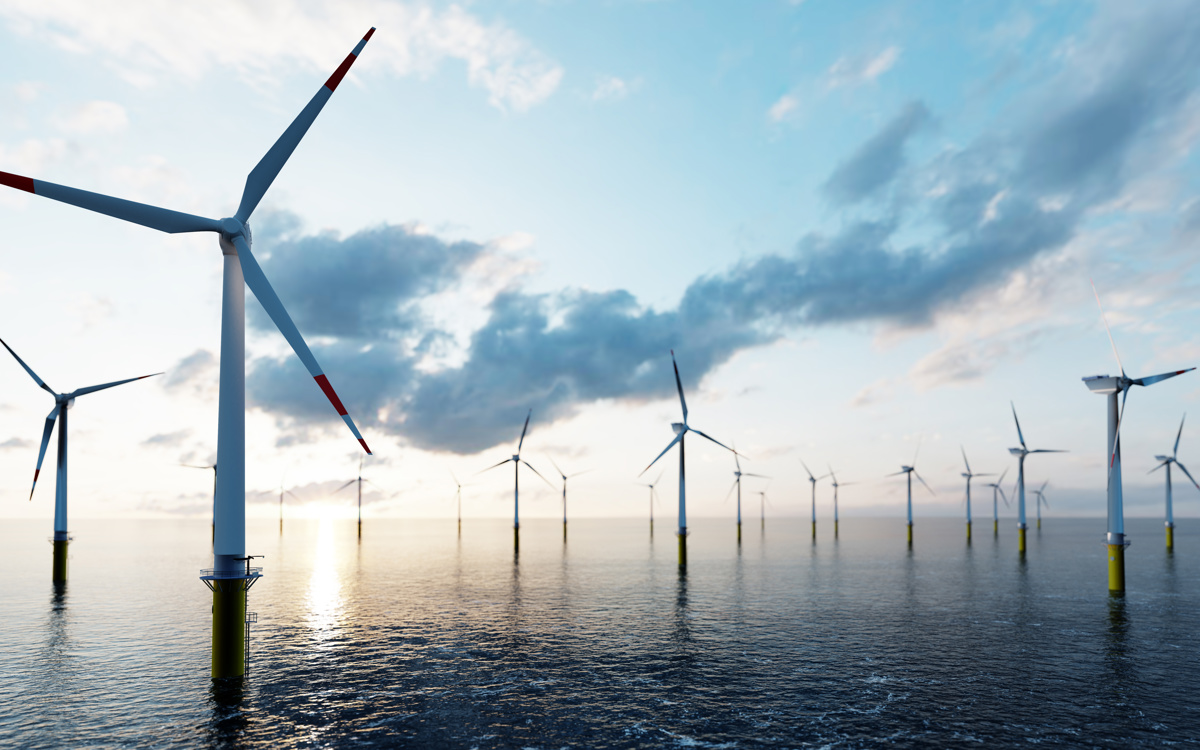
Next steps
To make this a reality, the enabling system needs to be defined and developed to prepare blades on wind farms for processing at a facility. The supply chain needs to make the following developments to be ready:
- Targeted onsite (or near site) cutting techniques: Necessary to isolate and remove carbon fibre composite sub-structures, such as spar caps.
- Define the shredding requirements: It is imperative that shredding is set up to provide feedstock for downstream processes that are governed by the industry pull.
- Spar cap and root section shredding capability: These sections are generally the thickest and strongest of the blade and the shredding equipment needs to be able to process them without a drop in throughput rate or excessive damage to the machinery.
- Utilising existing infrastructure (where possible): To accelerate development of the supply chain, infrastructure spending should be limited to upgrades that minimise material loss and ensure compliance with H&S legislation.
- Locality of supply chain: Accurate identification of key capabilities within the supply chain with the aim of minimising the economic and environmental impacts of transporting blade materials.
- Product disposal specifications (PDS) or materials passports (responsibility of OEMs): The efficiency of these operations will be greatly improved by the provision of blade specifications that detail each blade’s bill of material and internal structure. Without enough details the supply chain cannot separate material waste streams efficiently to enable a sustainable and cost-effective process. Whilst some PDS are being made available by blade OEMs in the DecomBlades consortium, the number of blade product lines referenced is severely limited and the material/structure data is scant. More transparency from the OEMs is required to increase the usefulness of these PDS.
Find out more about SusWIND’s evidence-based innovation for energy to support industrial transformation.