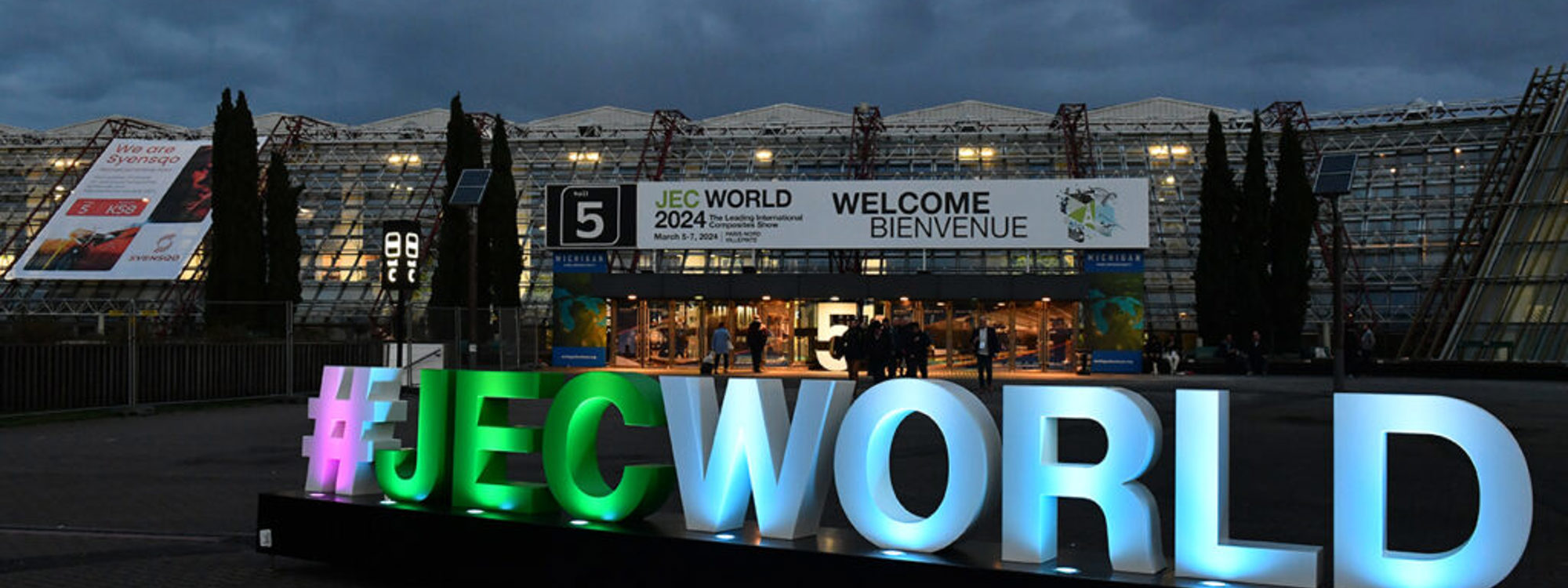
JEC World 2025 at Paris
NCC at JEC World 2025
Taking place 4-6 March 2025, Paris-Nord, Villepinte Exhibition Centre, Paris. Visit NCC on the UK Pavilion, managed by Composites UK, Hall 6, Booth T62.
Celebrating its 60th anniversary, this global trade show for composite materials and their applications. In line with JEC’s theme of “Pushing the Limits”, NCC’s focus is on innovation for sustainable transportation and distribution, showcasing our capabilities in advanced materials, sustainability, digital, hydrogen, energy and aerospace.
Visit our stand to engage with experts and demonstrators including a hydrogen tank and carbon fibre spool.
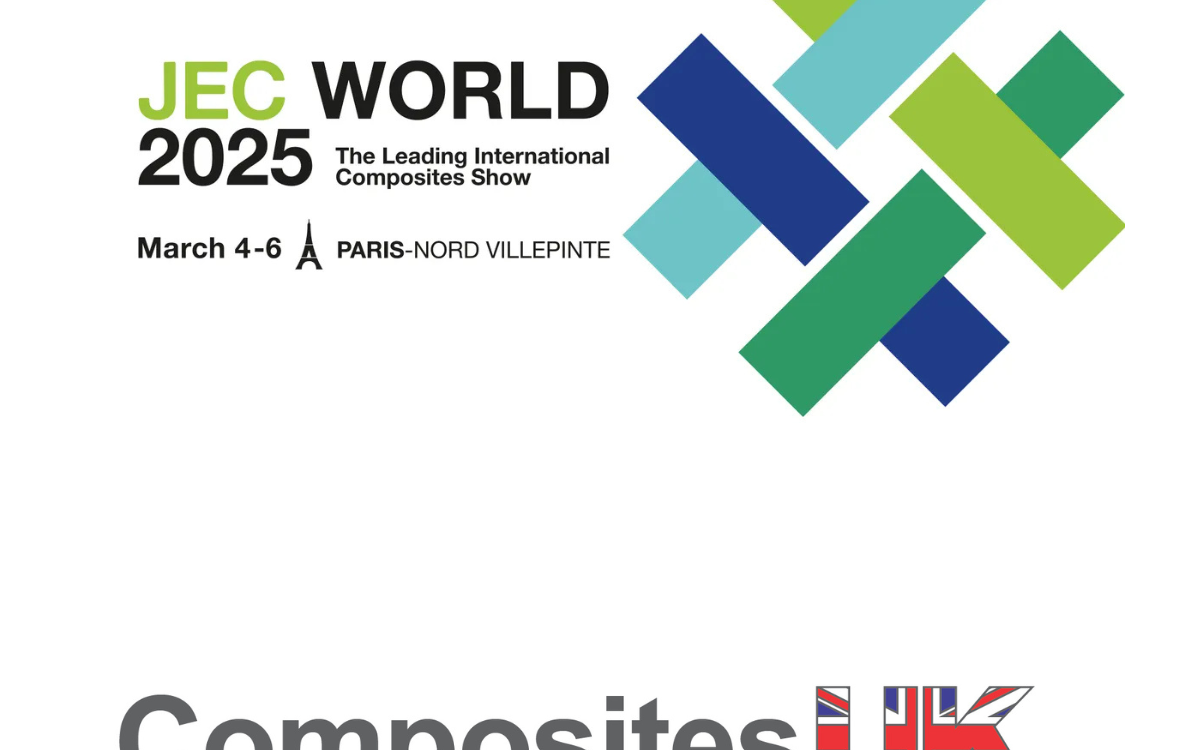
A host of NCC experts are available throughout the conference to discuss NCC’s end-to-end engineering capabilities and innovative solutions to meet your business needs include:
Sustainability, Technology, Digital
- Jack Alcock, Technology Development Lead [Stand team]
- Matt Scott, Chief Technologist for Strategy [Stand team]
- Itsaso Echeverria, Engineering Capability Lead for Materials & Processes [Stand team]
- Keith Bean, Engineering Capability Lead for Material Science [Stand team]
- Ashley Parkinson, SME Engagement Manager [Stand team]
- Kalyan Hazra, Head of Technology Integration
- Marisa Zeolla, Advanced Technology Project Lead
- Napapat Permpool, Research Engineer for Sustainability
Aerospace
- Andrew Bruton, Advanced Technology - Civil Aerospace Portfolio Manager [Stand team]
- Adrian Tayler, Head of Aerospace
- Andrew Limmack, Chief Engineer for Aerospace Propulsion
- Mark Bowering, Chief Engineer for Civil Air Structures
Energy
- Tom Andrews, Advanced Technology Project Lead for Energy [Stand team]
- Phil Slack, Head of Energy
- Jonathan Fuller, Principal Research Engineer for Energy
- Katherine McClearn, Research Engineer
Schedule time with our experts by emailing [email protected]
Alternatively, click ‘Talk to the team’ below, and complete the form.
Don’t miss our NCC speakers at the following sessions:
Our insight and impact
NCC’s innovation with industry explores radical new approaches towards enabling sustainable transportation and distribution.
NCC has announced the completion of the design phase for the UK’s new carbon fibre development lines, funded by the Department of Science Innovation and Technology’s ‘Research and Innovation Organisations Infrastructure Fund’.
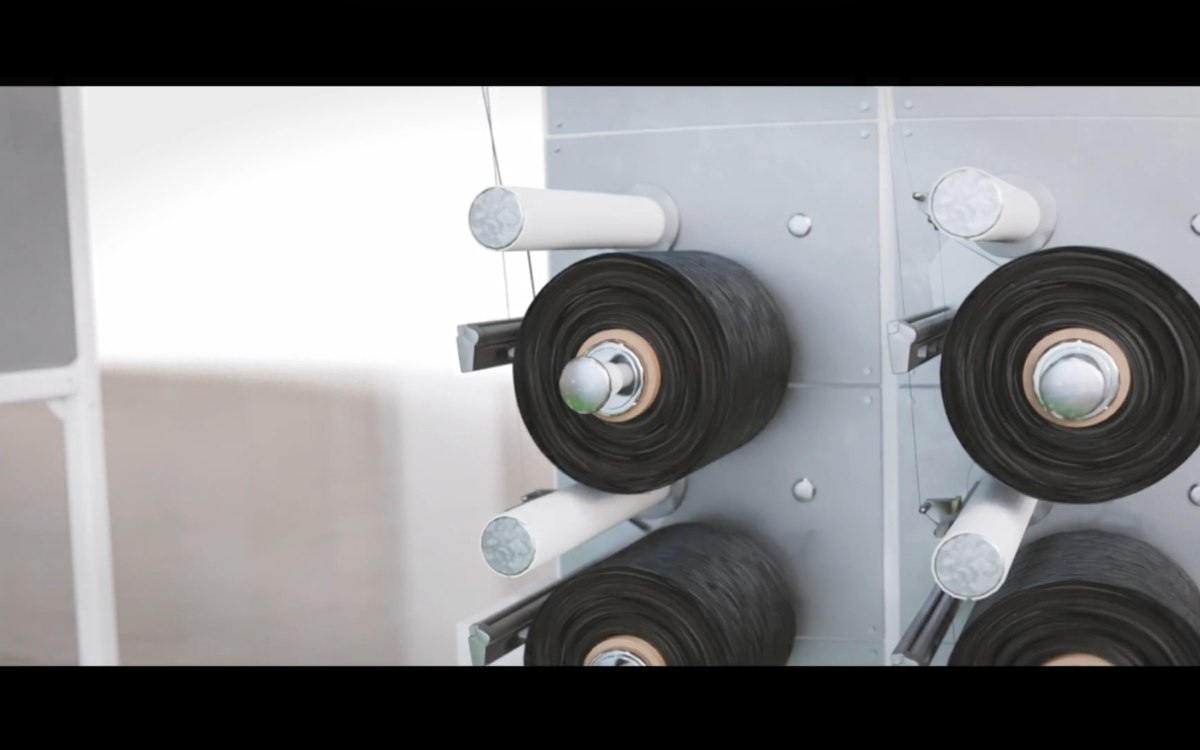
The innovations directly address a significant barrier to the adoption of recycled carbon fibre for high value applications.
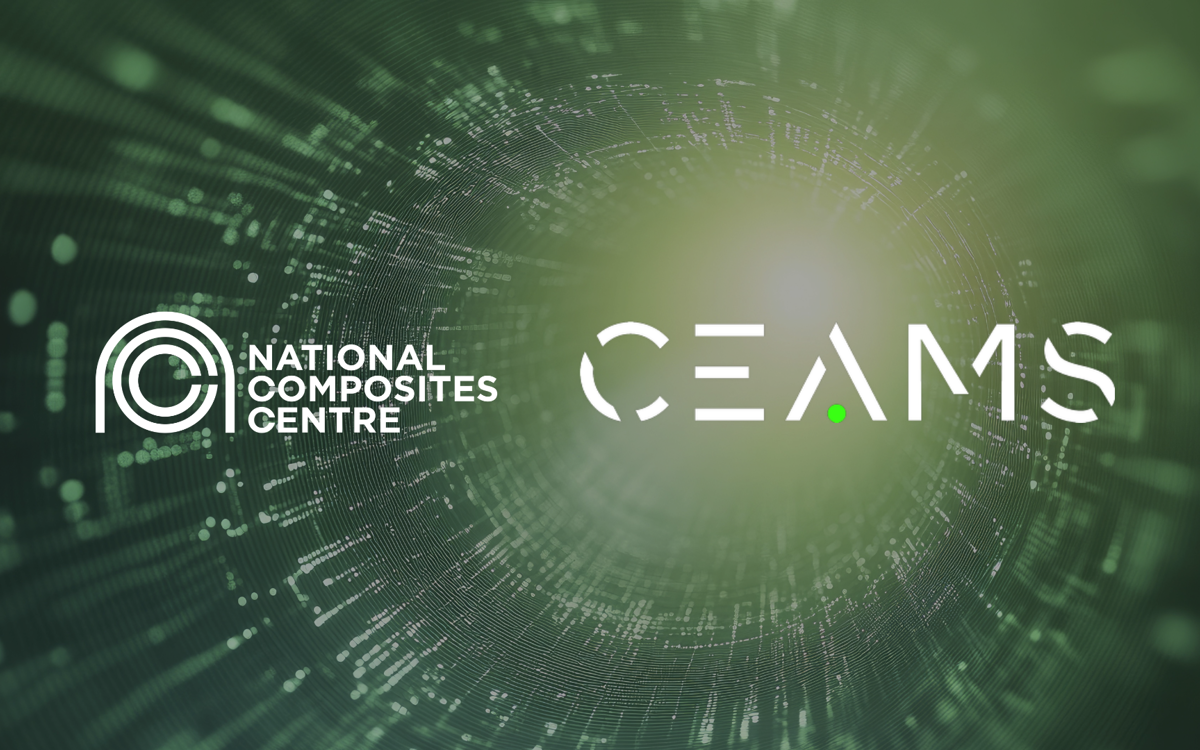
A new paper from the NCC sustainability team has been published in the Journal of Cleaner Production. Funded by SusWIND, it interrogates future strategies to identify a clear roadmap for carbon fibre decarbonisation.
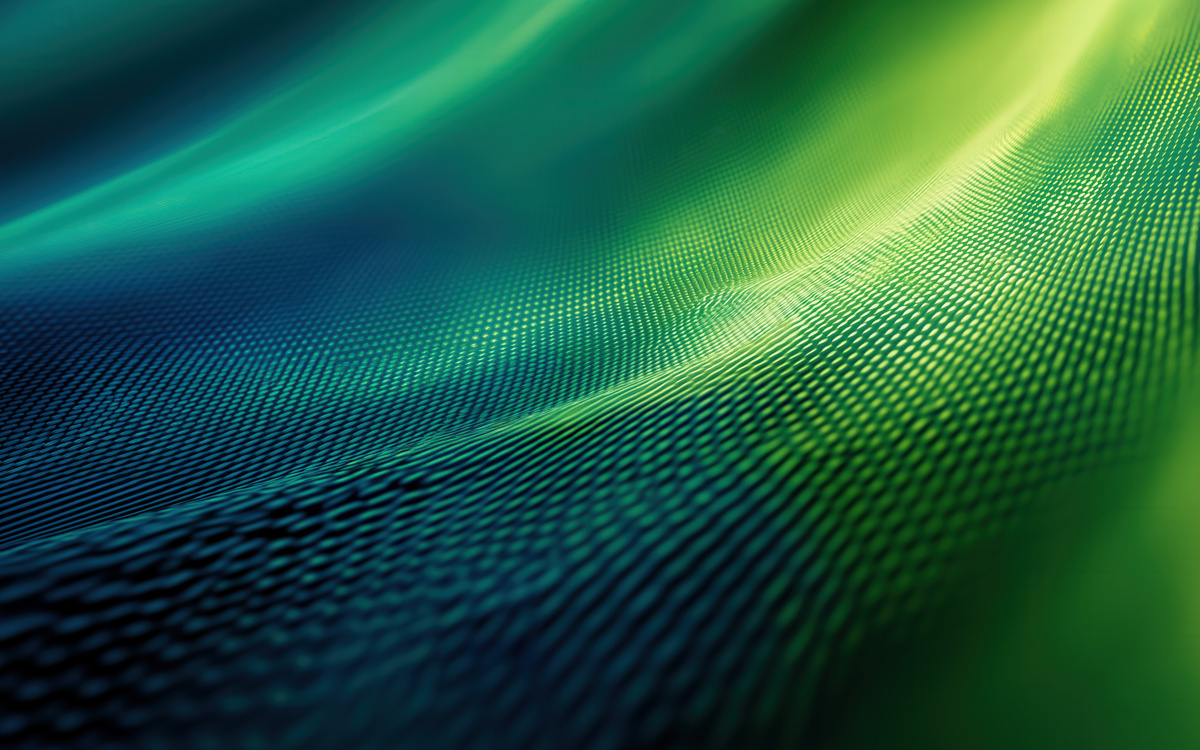
Using reclaimed continuous carbon fibres from a whole pressure vessel and re-using them to manufacture a new pressure vessel is a significant step in accelerating the clean energy transition.
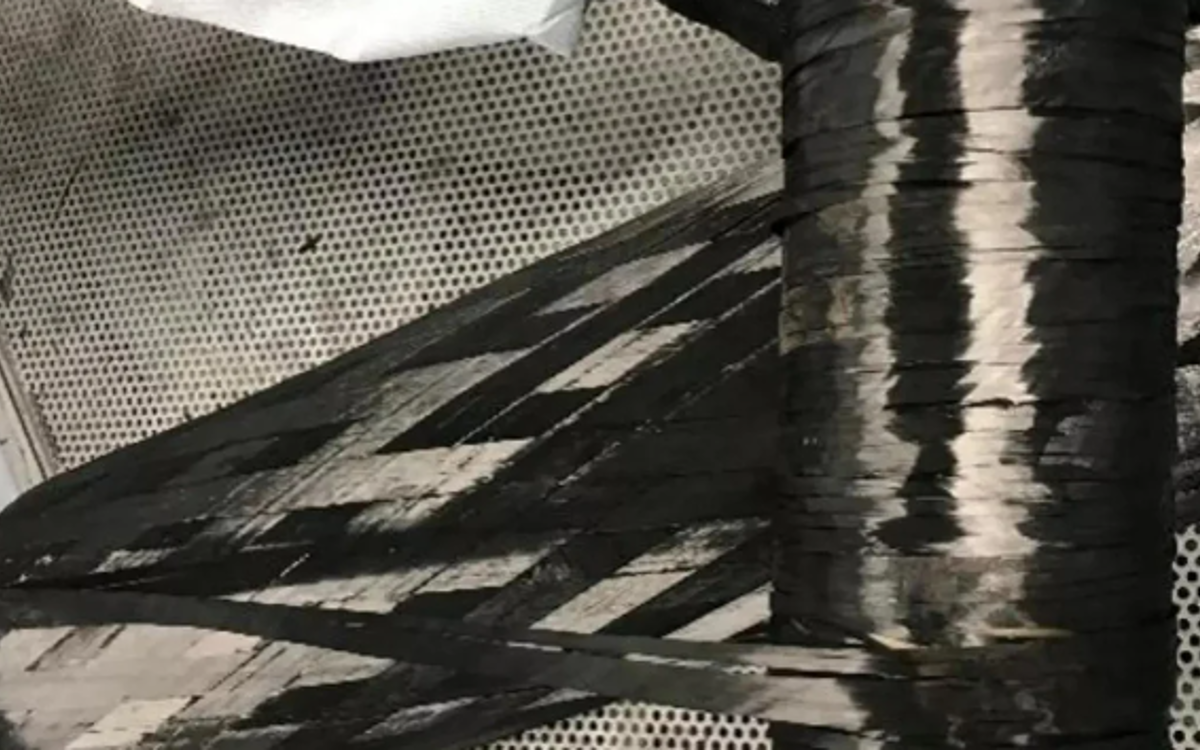
NCC has tested a range of composite cryogenic storage tanks with liquid hydrogen that it has designed and manufactured to support the UK’s transition to the hydrogen economy.
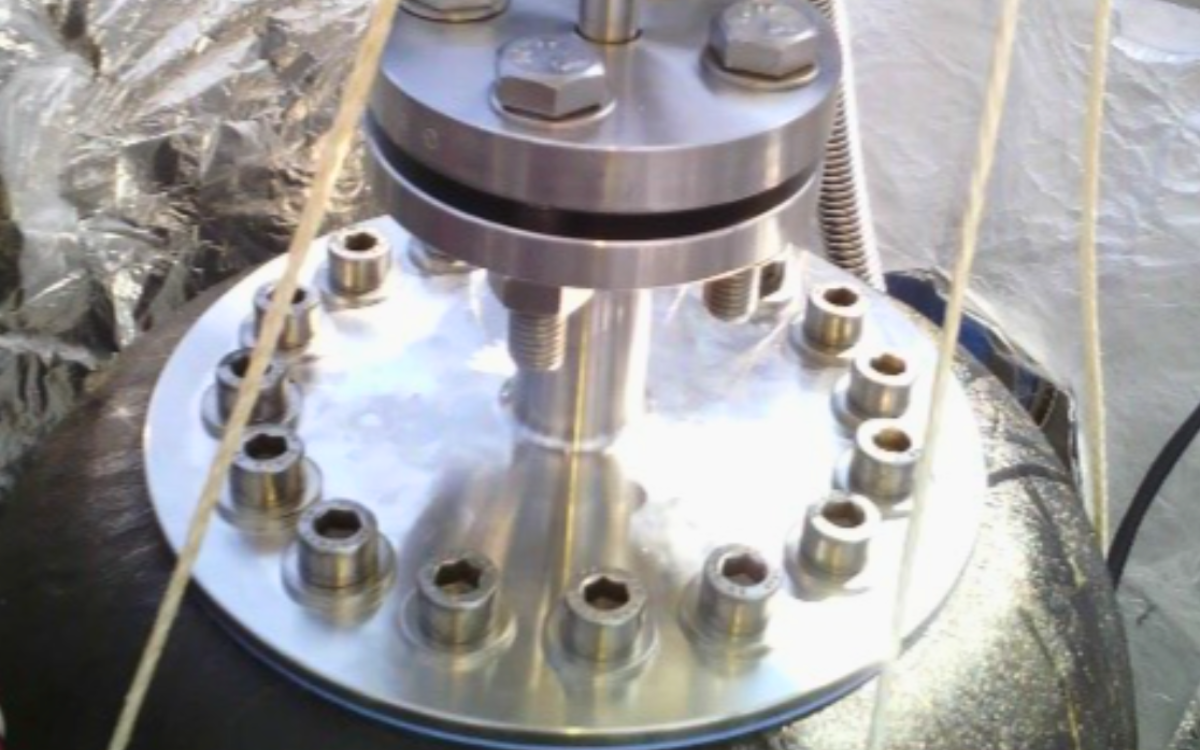
NCC’s joint industry programme with Offshore Renewable Energy Catapult is advancing a circular economy for large structure composites by driving innovation in recycling and sustainable supply chains.
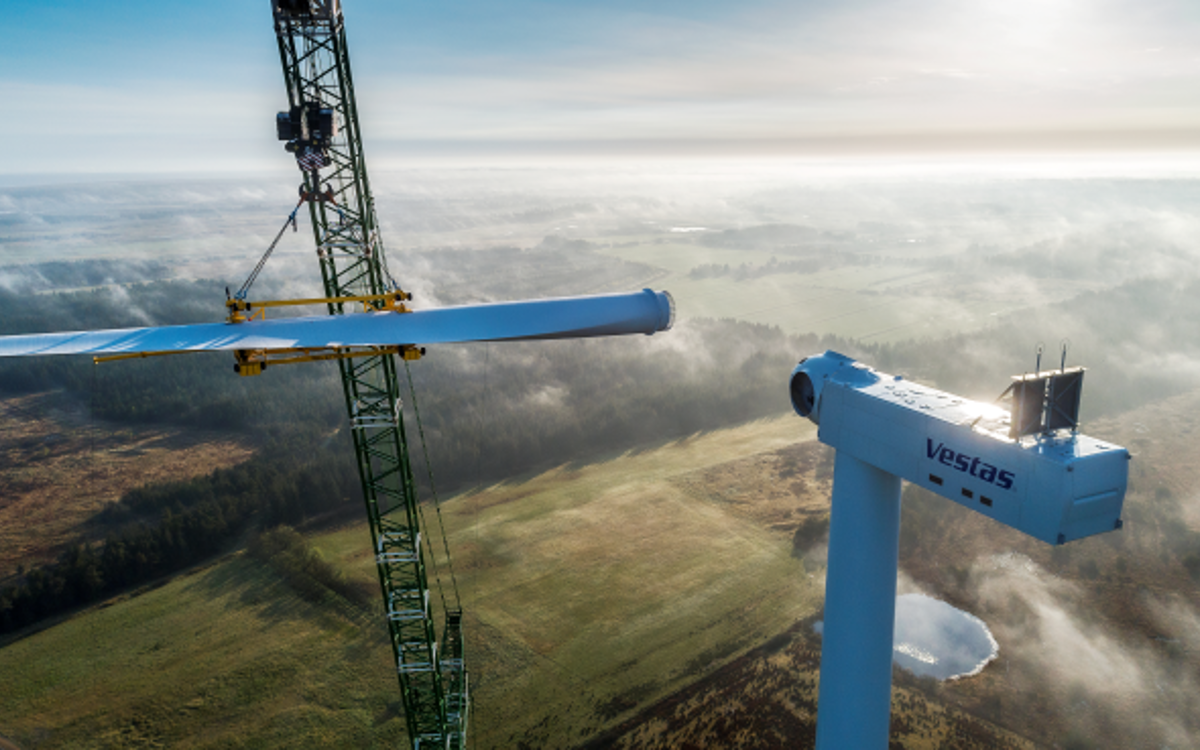
NCC helps UK SME extend medical imaging expertise into non-destructive testing (NDT) for the aviation industry, with the potential to break into a market estimated at £1.5 billion annually.
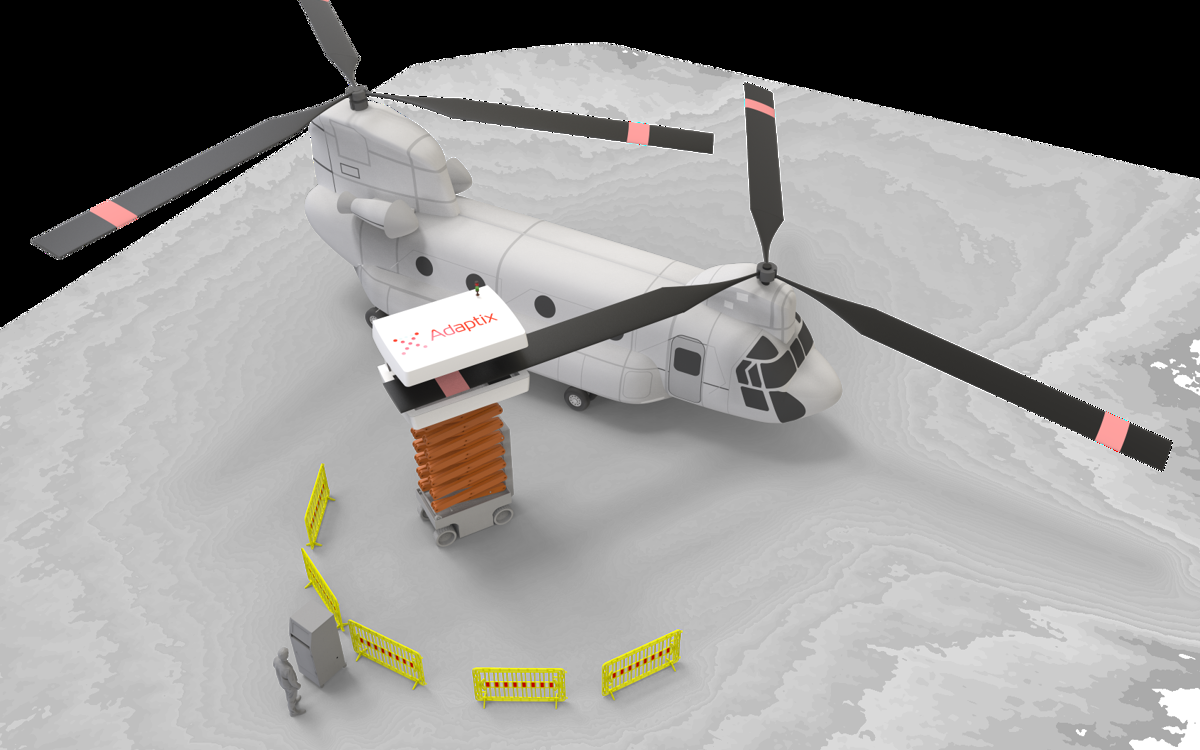
NCC supports Airbus’ innovative project to optimise wing aerodynamics and aircraft performance through hinged wingtips inspired by the biomimicry of seabirds.
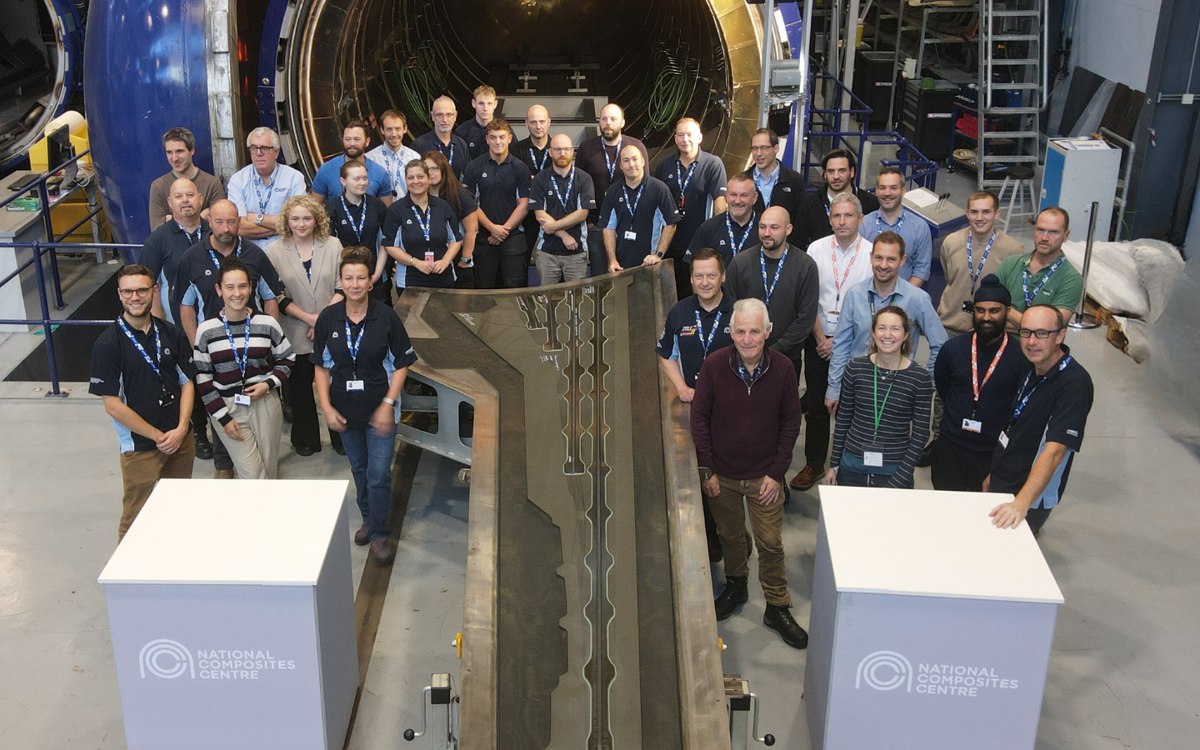
NCC’s expertise significantly contributed to the development of critical components for the VX4 electric aircraft prototype, and de-risking their path to certification.
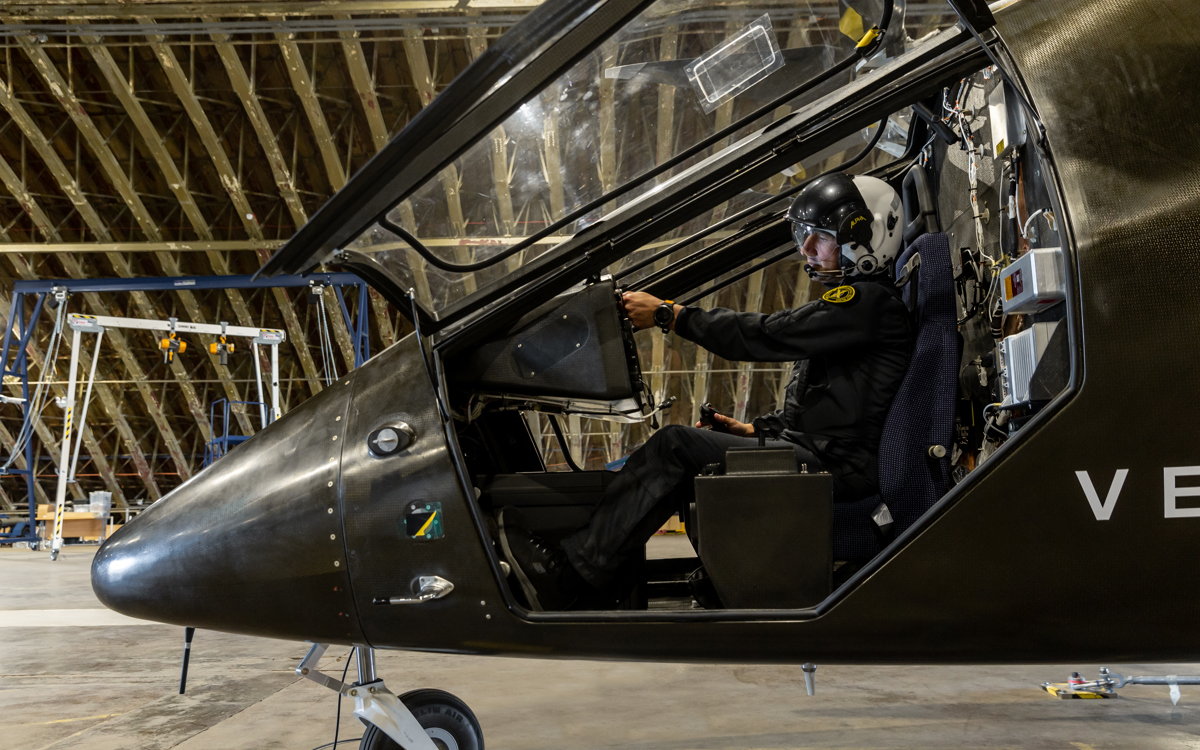
NCC achieves the world’s first full scale 17-metre integrated wing skin infused in one step.
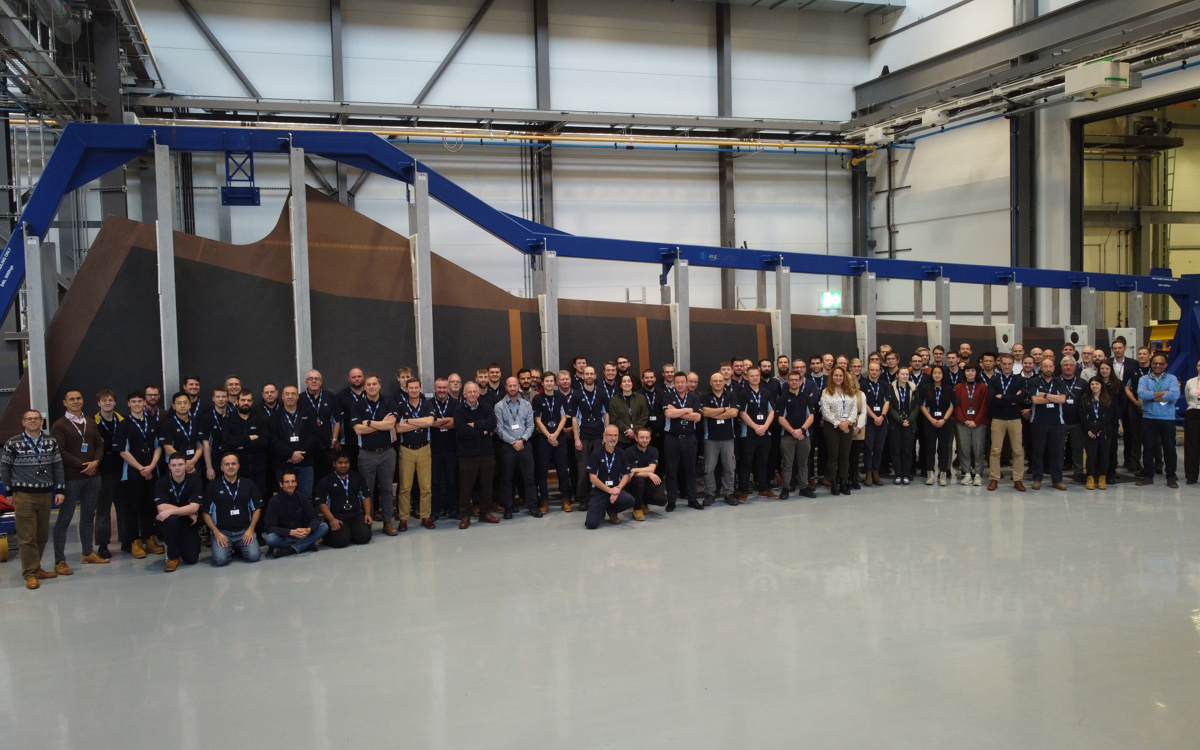
Our capabilities and innovation
Our tape winder and filament winder machines can create anything from high-strength pipes to high pressure type 4 hydrogen tanks. Our twin-ring braider can create components that are hollow and straight or complex cross sections with curved profiles.
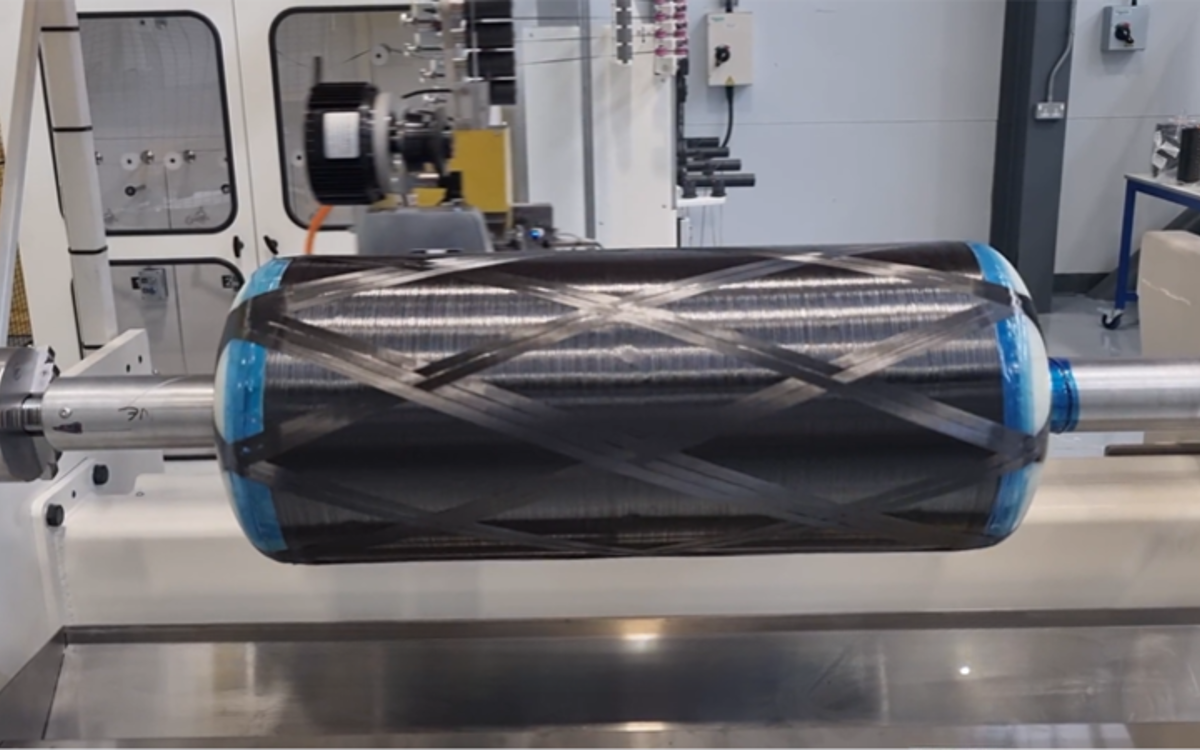
Our Ultra High Rate Deposition cell contains two huge industrial robots that automate the production process for future large scale, high rate composite products such as wings and turbine blades.
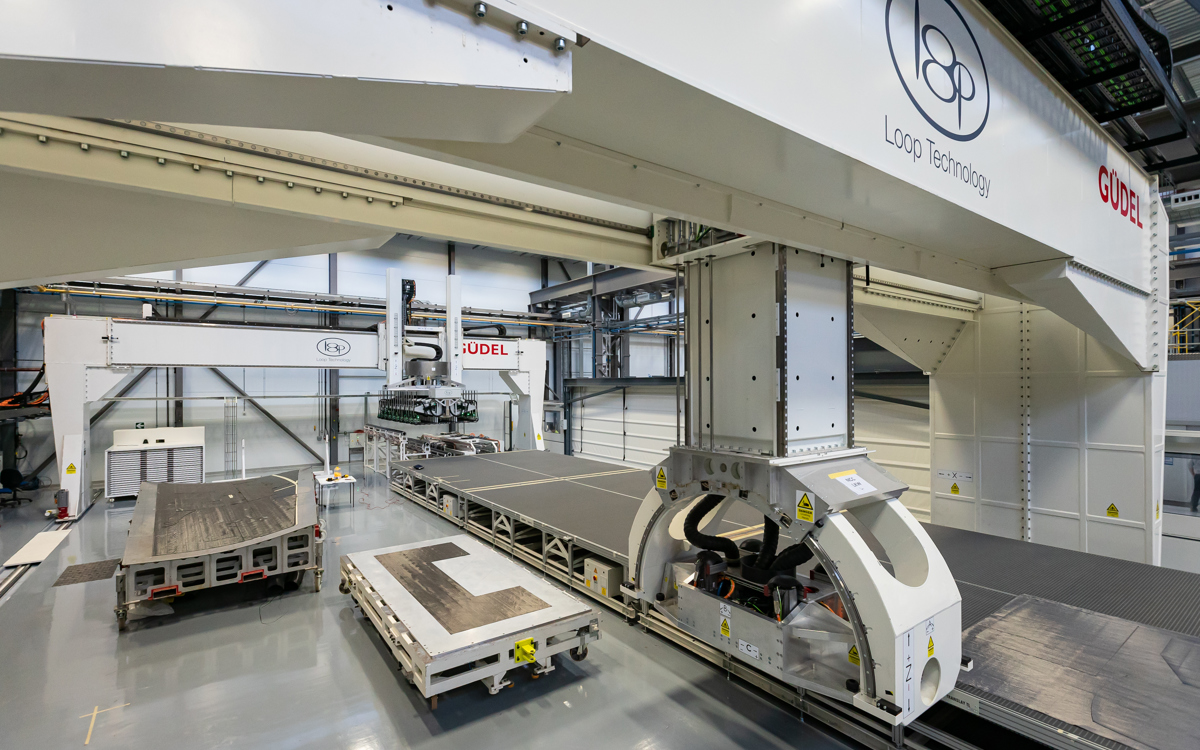
Our bespoke ceramic matrix composite (CMC) development facility includes material storage and processing equipment specifically for CMC applications, including aircraft propulsion.
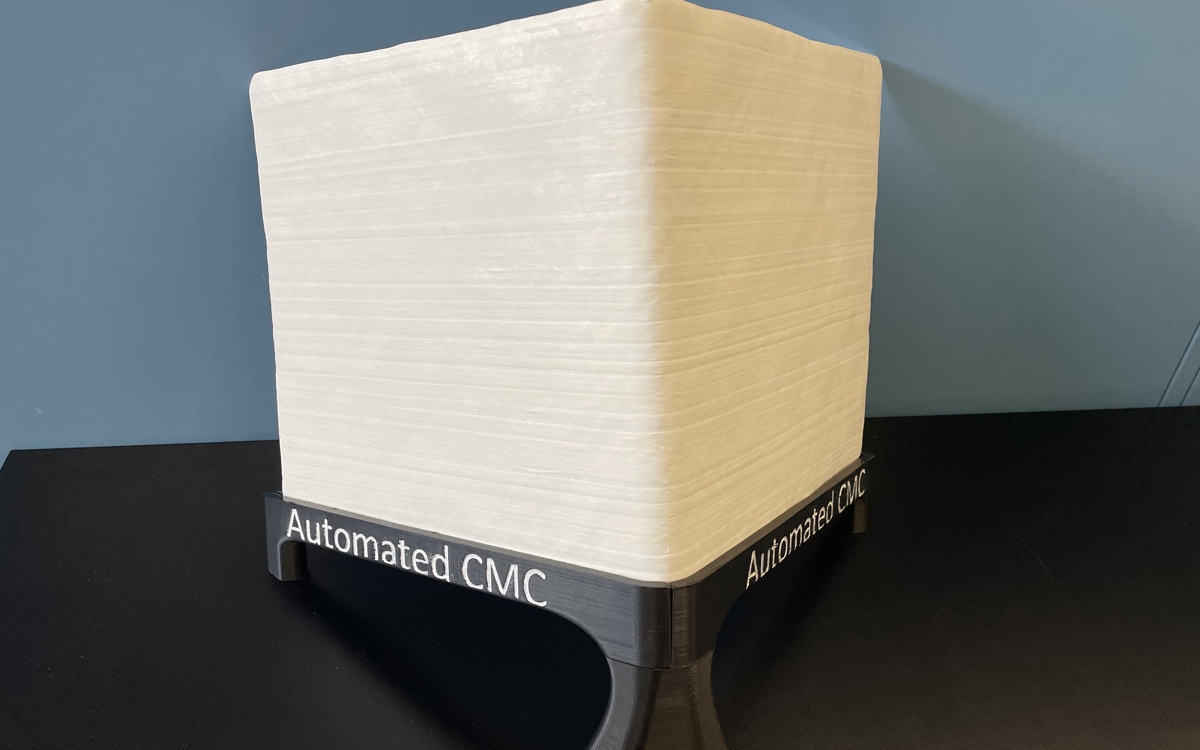
We are the best equipped research centre for automated fibre placement (AFP), tensioned fibre placement (TFP) and automated tape laying (ATL) in the world.
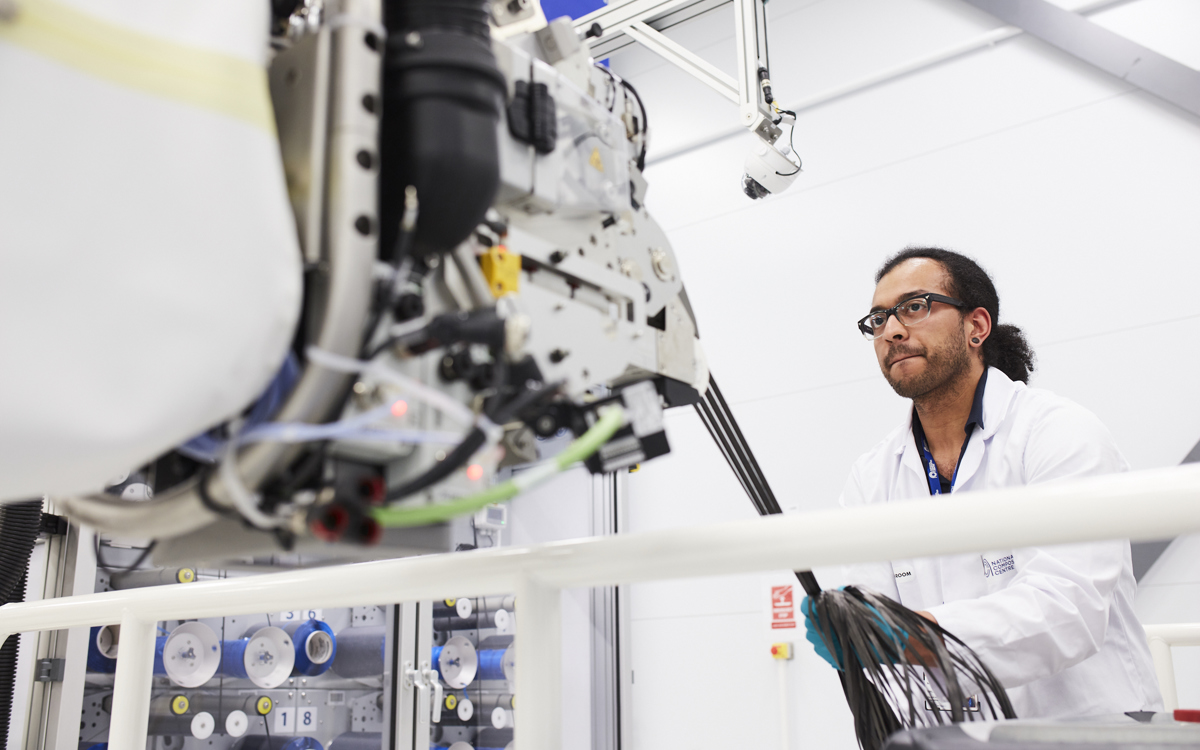
We have a suite of verification capabilities across non-destructive testing (NDT), metrology, and a materials testing laboratory to assess the quality and performance of a material or product.
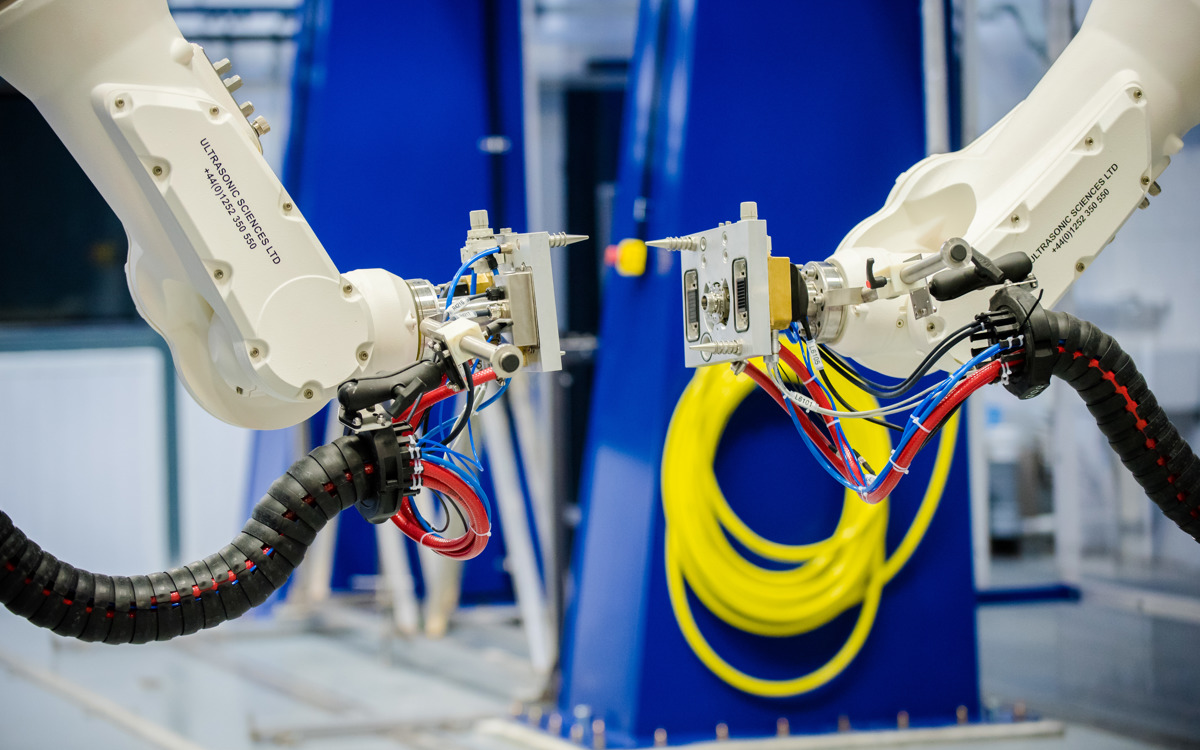
In addition to a range of specific automated manufacturing technologies, the NCC has a dedicated automation cell predominantly used to create fast, repeatable, complex parts. Our fixturing capabilities allow us to bond high precision parts into a safety critical assembly.
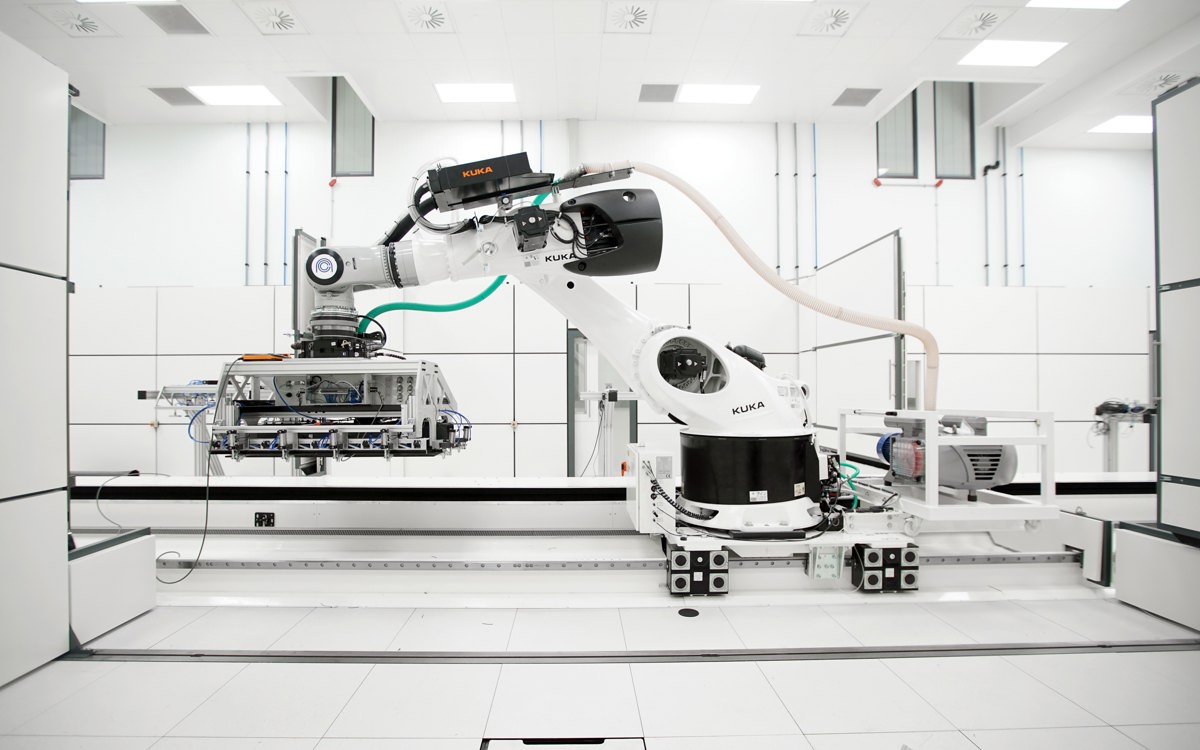
Our dedicated high volume manufacturing workshop is equipped with a range of presses, including our 3600T Schuler, and a state-of-the-art injection overmoulder capable of producing complex and repeatable parts in sub 5 minute cycle times.
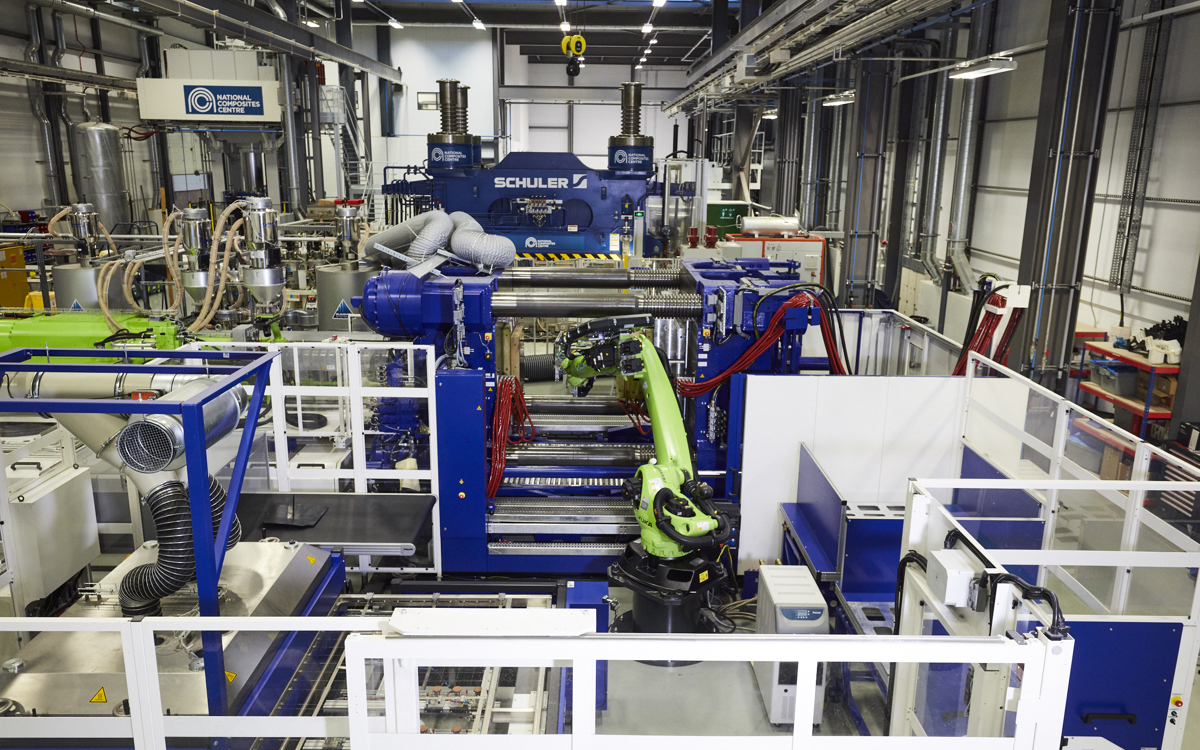
We have an array of resin infusion and resin transfer moulding capabilities that allow us to manufacture parts from 10s of millimetre up to 20 metre scale, and process materials at a range of temperatures and pressures.
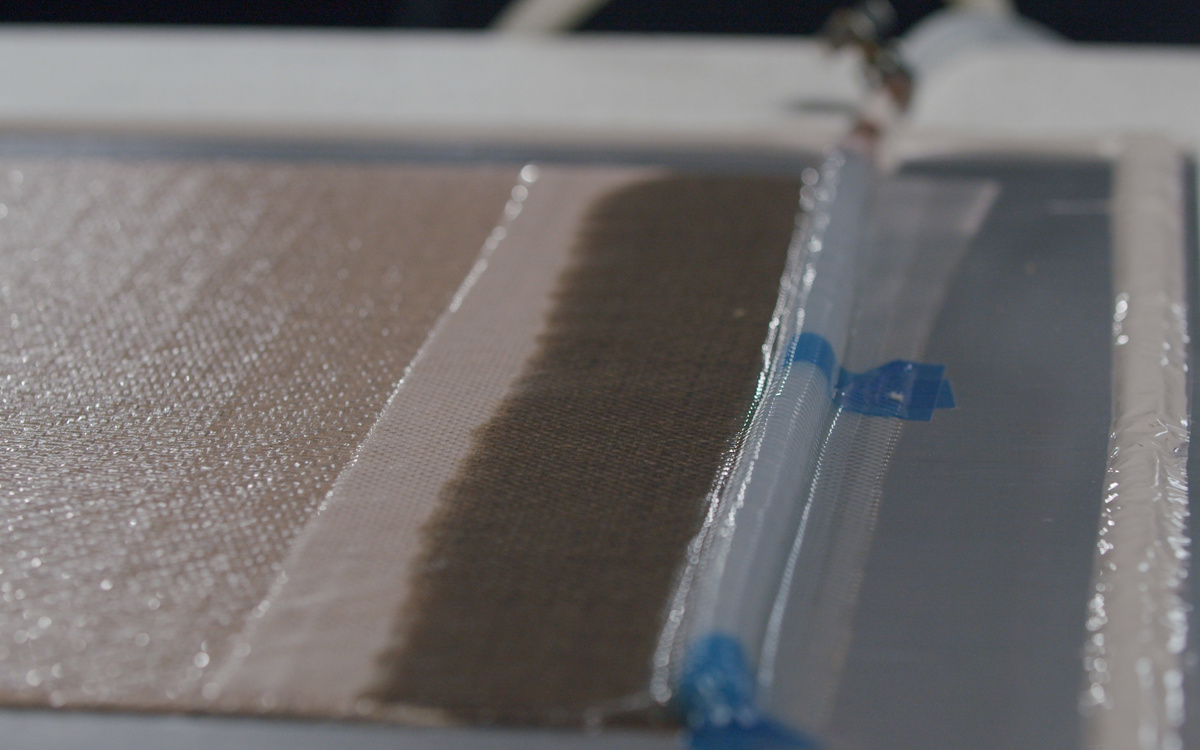
We have a wide variety of composite curing and assembly capabilities ranging from an oven or autoclave big enough to handle an aircraft wing to the fixturing and skills required to bond high-precision parts into a safety critical assembly.
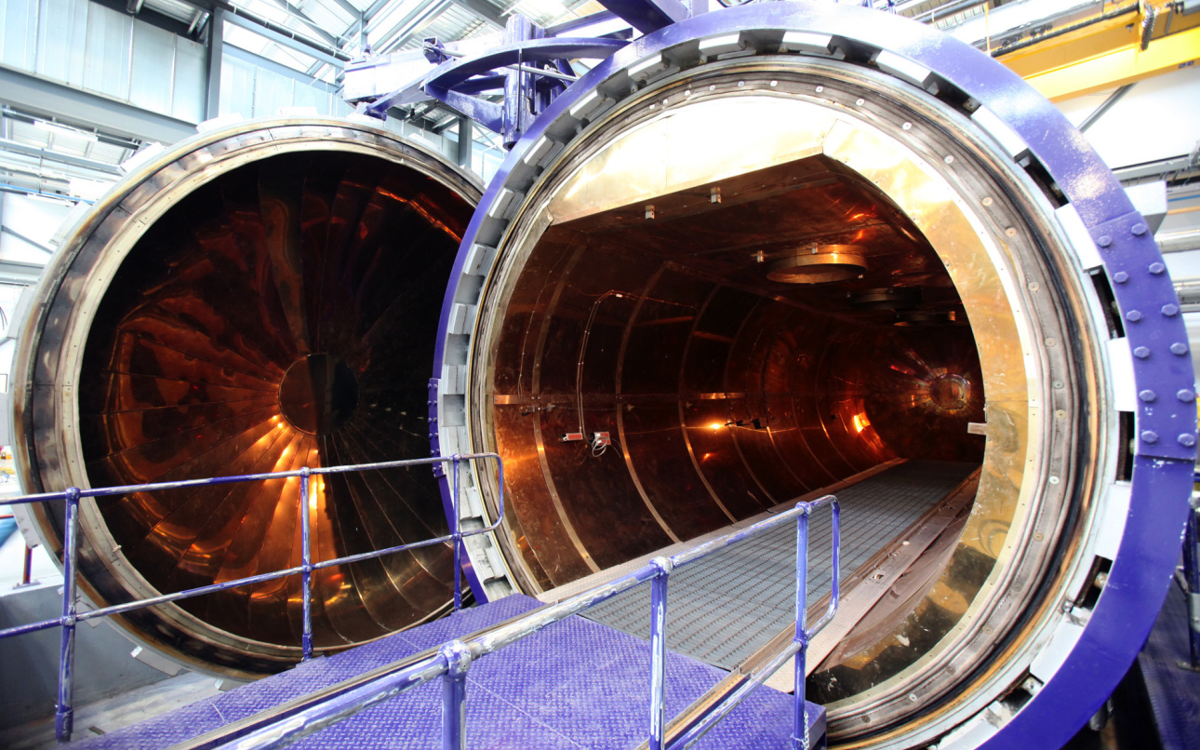
NCC’s novel cryostat screens a wide selection of materials at cryogenic temperatures. The low-cost method highlights the best candidates for detailed material testing using conventional methods.
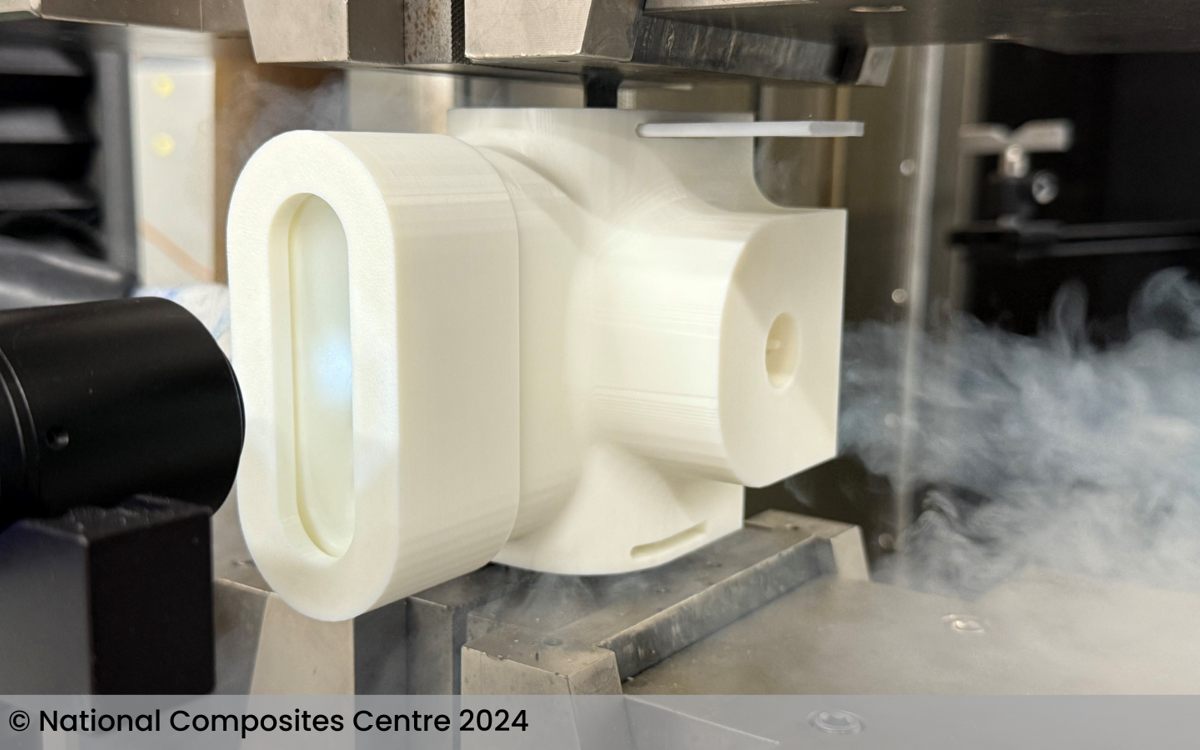